Automatic material collecting device for film cutting machine
A technology of automatic material receiving and film cutting machine, applied in thin material handling, transportation and packaging, metal processing, etc., can solve the problems of time-consuming and laborious manual material collection, film wear, low efficiency, etc., to improve material collection efficiency, reduce Wear and frictional resistance reduction effect
- Summary
- Abstract
- Description
- Claims
- Application Information
AI Technical Summary
Problems solved by technology
Method used
Image
Examples
Embodiment 1
[0042] see Figure 1-2 , an automatic material receiving device for a film cutting machine, comprising a film cutting table 1, a film cutting mechanism 2 is installed on the upper end of the film cutting table 1, a transmission crawler belt 3 and a feeding box 4 are installed on the right end of the film cutting table 1, and the feeding box 4 is positioned at the lower side of transmission crawler belt 3, and the right end of feeding box 4 is provided with inclined type receiving box 5, and the opening of inclined type receiving box 5 is flush with the lower side of driving crawler belt 3, and the upper end of feeding box 4 is provided with multiple There are a plurality of transfer balls 6 arranged in the supplementary groove, and a plurality of evenly distributed accommodation grooves are provided on the surface of the transmission crawler 3, and the accommodation grooves match the transfer balls 6, and there are multiple transmission balls 6 in the transmission crawler 3. A...
PUM
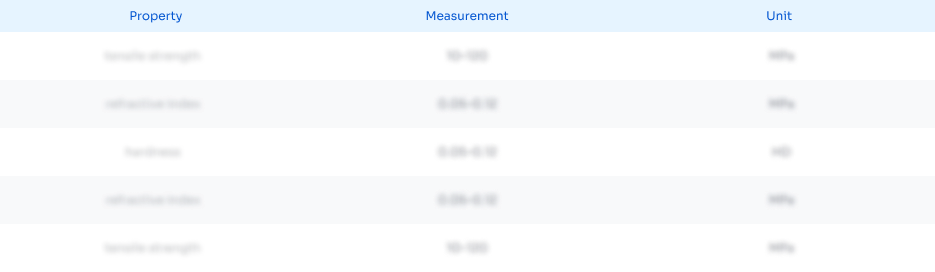
Abstract
Description
Claims
Application Information

- R&D
- Intellectual Property
- Life Sciences
- Materials
- Tech Scout
- Unparalleled Data Quality
- Higher Quality Content
- 60% Fewer Hallucinations
Browse by: Latest US Patents, China's latest patents, Technical Efficacy Thesaurus, Application Domain, Technology Topic, Popular Technical Reports.
© 2025 PatSnap. All rights reserved.Legal|Privacy policy|Modern Slavery Act Transparency Statement|Sitemap|About US| Contact US: help@patsnap.com