Production process method of polaroid
A production process and polarizer technology, applied in manufacturing tools, laser welding equipment, metal processing equipment, etc., can solve the problems of a large number of coding mechanisms, low product yield, poor quality of finished products, etc., to achieve fully automated operations, High product yield and good product quality
- Summary
- Abstract
- Description
- Claims
- Application Information
AI Technical Summary
Problems solved by technology
Method used
Image
Examples
preparation example Construction
[0062] This application adopts the preparation process of cutting first and then spraying codes. First, the material is cut into multiple sheets by the laser cutting mechanism 2, and then each sheet is sprayed by the coding mechanism 3, thereby reducing the cost of the coding mechanism 3. quantity, thereby reducing costs. The laser cutting mechanism 2 cuts the roll material by laser. Compared with blade cutting, laser cutting has fewer burrs and better product quality; moreover, laser cutting is highly efficient in preparing special-shaped polarizers that need to be punched or slotted. The automatic feeding operation of coil materials can be realized through the feeding mechanism 1; the quality inspection of each sheet can be carried out through a plurality of detection mechanisms 4, thereby improving the product yield. Through the integration of feeding mechanism 1, laser cutting mechanism 2, coding mechanism 3 and multiple detection mechanisms 4, the production of polarizers...
specific Embodiment approach
[0070] In one example, see figure 2 with image 3 , as a specific implementation of the production process method of the polarizer provided in the embodiment of the present application, the step of cleaning S5 also includes:
[0071] Deviation Correction S56: Use the deviation rectification mechanism 56 to correct the position of each sheet after the second scrubbing.
[0072] With this structure, the position of the sheet after the secondary scrubbing can be corrected by the deviation correcting mechanism 56, which facilitates the detection of each sheet by the subsequent detection mechanism 4, helps to improve the detection accuracy, and further improves the product yield.
[0073] In one example, see figure 2 with image 3 , as a specific implementation of the production process method of the polarizer provided in the embodiment of the present application, the step of cleaning S5 also includes:
[0074] Dedusting S57 : dedusting the cleaned sheets by the dedusting mecha...
PUM
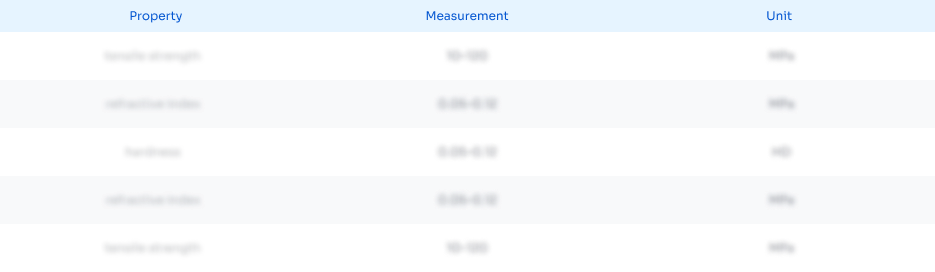
Abstract
Description
Claims
Application Information

- Generate Ideas
- Intellectual Property
- Life Sciences
- Materials
- Tech Scout
- Unparalleled Data Quality
- Higher Quality Content
- 60% Fewer Hallucinations
Browse by: Latest US Patents, China's latest patents, Technical Efficacy Thesaurus, Application Domain, Technology Topic, Popular Technical Reports.
© 2025 PatSnap. All rights reserved.Legal|Privacy policy|Modern Slavery Act Transparency Statement|Sitemap|About US| Contact US: help@patsnap.com