Method for quickly positioning and measuring dead load condition of in-service bridge structure
A bridge structure, positioning measurement technology, applied in the field of bridge structure, can solve problems such as time-consuming, dependence on professional quality and subjective judgment, lack of quantitative scientific basis, etc., to improve the efficiency of measurement and control, and quickly calculate the structure size.
- Summary
- Abstract
- Description
- Claims
- Application Information
AI Technical Summary
Problems solved by technology
Method used
Image
Examples
Embodiment Construction
[0028] The following is attached Figure 1-9 The present invention is described in further detail.
[0029] refer to figure 1 As shown, the embodiment of the present invention provides a method for quickly locating and measuring the dead load condition of an in-service bridge structure using three-dimensional laser scanning technology combined with local scale measurement, including the following steps;
[0030] S1. On-site layout of measurement and control points and reference points according to the structural geometry; the measurement and control points include: external measurement and control points of the structure and internal measurement and control points of the structure; the reference points are three absolute references arranged at preset distances around the adjacent structure Points P1~P3, based on the total station to construct an absolute coordinate system (OXYZ) for the three absolute reference points P1~P3 A , and collect the coordinate data of three absolu...
PUM
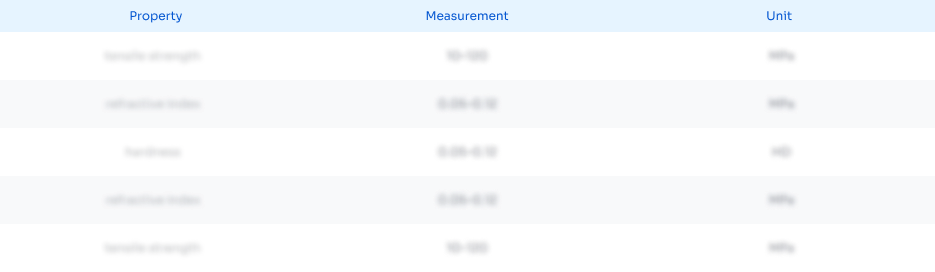
Abstract
Description
Claims
Application Information

- R&D
- Intellectual Property
- Life Sciences
- Materials
- Tech Scout
- Unparalleled Data Quality
- Higher Quality Content
- 60% Fewer Hallucinations
Browse by: Latest US Patents, China's latest patents, Technical Efficacy Thesaurus, Application Domain, Technology Topic, Popular Technical Reports.
© 2025 PatSnap. All rights reserved.Legal|Privacy policy|Modern Slavery Act Transparency Statement|Sitemap|About US| Contact US: help@patsnap.com