Non-contact phase difference type torque sensing device
A torque sensing, non-contact technology, applied in the direction of measuring devices, torque measurement, power measurement, etc., can solve the problems of difficult wired connection sensors, high cost, complex signal transmission technology, etc., to achieve simple signal transmission, low cost, The effect of technical simplification
- Summary
- Abstract
- Description
- Claims
- Application Information
AI Technical Summary
Problems solved by technology
Method used
Image
Examples
Embodiment Construction
[0030] The technical solution of the present invention will be further described below in conjunction with the accompanying drawings.
[0031] Such as figure 1 , figure 2 As shown, the non-contact phase difference torque sensing device of the present invention includes a central axis 1, a torsion bar 4, an input-side grating 5, an output-side grating 3, an output end and a sensor 8; pedals are respectively provided at both ends of the central axis 1, As a power input; such as figure 2 As shown, the torsion bar 4 is divided into two parts, one part is connected with the central shaft 1 through a spline, and the other part is connected with the output end. The part connected with the center shaft 1 is provided with an input-side grating 5, and the part connected with the clutch 9 or other output parts is provided with an output-side grating 3. The sensor 8 cooperates with the input-side grating 5 and the output-side grating 3 to detect the phase difference between the input...
PUM
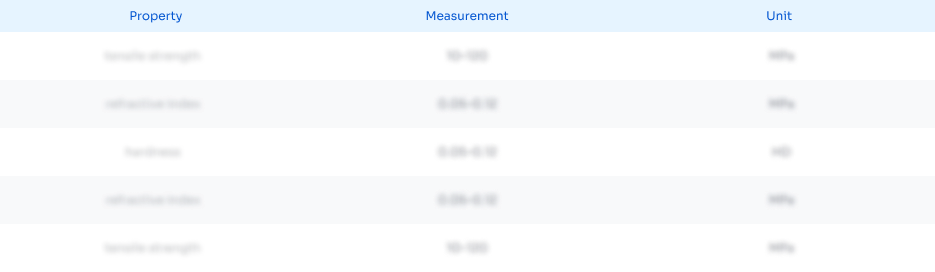
Abstract
Description
Claims
Application Information

- R&D Engineer
- R&D Manager
- IP Professional
- Industry Leading Data Capabilities
- Powerful AI technology
- Patent DNA Extraction
Browse by: Latest US Patents, China's latest patents, Technical Efficacy Thesaurus, Application Domain, Technology Topic, Popular Technical Reports.
© 2024 PatSnap. All rights reserved.Legal|Privacy policy|Modern Slavery Act Transparency Statement|Sitemap|About US| Contact US: help@patsnap.com