A Quasi-zero Stiffness Absolute Displacement Sensor Based on Electromagnetic Positive Stiffness
A displacement sensor, quasi-zero stiffness technology, applied in the direction of using electromagnetic means, instruments, electrical devices, etc., can solve the problems of lack of measurement objects, unachievable time response, affecting measurement accuracy, etc., to eliminate nonlinear effects, The effect of reducing the overall stiffness and reducing the volume of the mechanism
- Summary
- Abstract
- Description
- Claims
- Application Information
AI Technical Summary
Problems solved by technology
Method used
Image
Examples
Embodiment Construction
[0055] The following will clearly and completely describe the technical solutions in the embodiments of the present invention with reference to the accompanying drawings in the embodiments of the present invention. Obviously, the described embodiments are only some, not all, embodiments of the present invention. Based on the embodiments of the present invention, all other embodiments obtained by persons of ordinary skill in the art without making creative efforts belong to the protection scope of the present invention.
[0056] Such as Figures 1 to 21 As shown, this embodiment provides a quasi-zero stiffness absolute displacement sensor based on electromagnetic positive stiffness, including an eddy current displacement sensor unit, a negative stiffness unit, an intermediate connecting body, a positive stiffness unit, and a bottom shell sequentially connected from top to bottom ; Also includes a movement shaft that runs through the negative stiffness unit, the intermediate con...
PUM
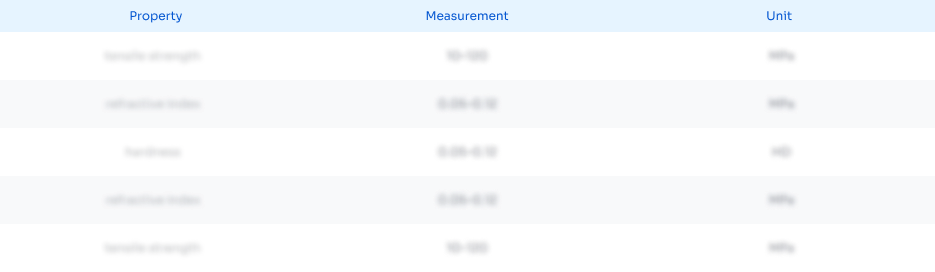
Abstract
Description
Claims
Application Information

- R&D
- Intellectual Property
- Life Sciences
- Materials
- Tech Scout
- Unparalleled Data Quality
- Higher Quality Content
- 60% Fewer Hallucinations
Browse by: Latest US Patents, China's latest patents, Technical Efficacy Thesaurus, Application Domain, Technology Topic, Popular Technical Reports.
© 2025 PatSnap. All rights reserved.Legal|Privacy policy|Modern Slavery Act Transparency Statement|Sitemap|About US| Contact US: help@patsnap.com