Manufacturing method of separation gate power MOSFET device
A manufacturing method and separation gate technology, which are used in semiconductor/solid-state device manufacturing, semiconductor devices, electrical components, etc.
- Summary
- Abstract
- Description
- Claims
- Application Information
AI Technical Summary
Problems solved by technology
Method used
Image
Examples
Embodiment 1
[0040] like image 3 As shown, a method for manufacturing a split gate power MOSFET device includes the following steps:
[0041] 1) A series of groove structures are formed on the epitaxial layer, and a first dielectric layer is formed on the inner wall of the groove structure;
[0042] 2) depositing polysilicon in the groove structure so that the polysilicon fills the entire groove;
[0043] 3) The polysilicon deposited in the etching step 2) forms the lower half of the stepped separation gate electrode in the control gate groove of the active region;
[0044] 4) wet etching the first dielectric layer, then depositing polysilicon in the groove structure, so that the polysilicon fills the entire groove;
[0045] 5) The polysilicon deposited in the etching step 4) forms the upper half of the stepped separation gate electrode in the control gate groove of the active region;
[0046] 6) depositing and etched back to form a second dielectric layer in the groove of the active reg...
Embodiment 2
[0061] like Figure 4 As shown, this embodiment provides some steps of a method for manufacturing a split-gate power MOSFET device, which is used to replace image 3 In the (j)-(k) process, the difference between this embodiment and the manufacturing method described in Embodiment 1 is that step 9) can be implemented as follows:
[0062] 9) dry etching the oxide layer, controlling the etched interface to keep a certain distance from the upper interface of the stepped separation gate; then wet etching away the remaining silicon nitride in the groove;
Embodiment 3
[0064] like Figure 5 As shown, the difference between this embodiment and the manufacturing method described in Embodiment 1 is that the first dielectric layer formed in step 1) surrounding the separated gate electrode adopts a low-k material with k less than 3.9 instead of silicon dioxide, which can further reduce the source-drain capacitance.
PUM
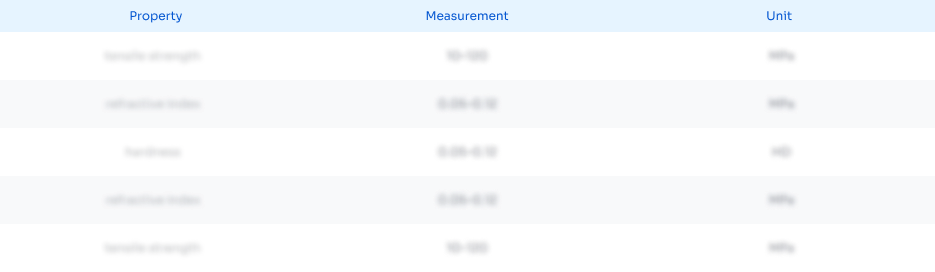
Abstract
Description
Claims
Application Information

- R&D Engineer
- R&D Manager
- IP Professional
- Industry Leading Data Capabilities
- Powerful AI technology
- Patent DNA Extraction
Browse by: Latest US Patents, China's latest patents, Technical Efficacy Thesaurus, Application Domain, Technology Topic, Popular Technical Reports.
© 2024 PatSnap. All rights reserved.Legal|Privacy policy|Modern Slavery Act Transparency Statement|Sitemap|About US| Contact US: help@patsnap.com