Composite polyurethane foam emulsion separation material, and preparation method and application thereof
A composite polyurethane and polyurethane foam technology, which is applied in separation methods, liquid separation, chemical instruments and methods, and can solve problems such as secondary pollution, easy deactivation, and cumbersome preparation processes
- Summary
- Abstract
- Description
- Claims
- Application Information
AI Technical Summary
Problems solved by technology
Method used
Image
Examples
Embodiment 1
[0048] This embodiment provides a composite polyurethane foam emulsion separation material, which is prepared by the following method:
[0049] Step 1: Stir and mix 50mL of polytetrahydrofuran diol, 220uL of A33, 160uL of T-9, 1500uL of L-580, 2855uL of ultrapure water, 3552uL of dichloromethane, and 1g of polyaluminum chloride. The stirring speed is 1500r / min, the stirring time is 8min.
[0050] Step 2: Add 34.85 mL of toluene diisocyanate to the mixture prepared in step 1, and increase the stirring speed at the same time, the stirring speed is 4500 r / min, and the stirring time is 15 s.
[0051] Step 3, transfer the reactant in step 2 to a foaming mold, and allow it to foam freely for 3 minutes.
[0052] Step 4: After the reactants in step 3 are foamed, transfer them together with the foaming mold to an open place, allowing them to mature and stabilize under natural conditions for 24 hours.
Embodiment 2
[0054] This embodiment provides a composite polyurethane foam emulsion separation material, which is prepared by the following method:
[0055] Step 1, 50mL of polypropylene oxide triol, A1 is 210uL, T-22 is 145uL, L-618 is 1200uL, ultrapure water 2950uL, dichloromethane 3258uL, polyaluminum chloride 2g are stirred and mixed, and the stirring speed is 1800r / min, stirring time is 8min.
[0056] Step 2: Add 35.45 mL of toluene diisocyanate to the mixture prepared in step 1, and increase the stirring speed at the same time, the stirring speed is 4800 r / min, and the stirring time is 15 s.
[0057] Step 3, transfer the reactant in step 2 to a foaming mold, and allow it to foam freely for 4 minutes.
[0058] Step 4: After the reactants in step 3 are foamed, transfer them together with the foaming mold to an open place, allowing them to mature and stabilize under natural conditions for 24 hours.
Embodiment 3
[0060] This embodiment provides a composite polyurethane foam emulsion separation material, which is prepared by the following method:
[0061] Step 1, 50mL of polytetrahydrofuran diol, A107 is 180uL, T-9 is 140uL, SC154 is 1150uL, ultrapure water 2625uL, dichloromethane 3872uL, polyaluminum chloride 3g are stirred and mixed, the stirring speed is 2000r / min, Stirring time is 10min.
[0062] Step 2: Add 33.34 mL of toluene diisocyanate to the mixture prepared in step 1, and increase the stirring speed at the same time, the stirring speed is 5000 r / min, and the stirring time is 15 s.
[0063] Step 3, transfer the reactant in step 2 to a foaming mold, and allow it to foam freely for 5 minutes.
[0064] Step 4: After the reactants in step 3 are foamed, transfer them together with the foaming mold to an open place, allowing them to mature and stabilize under natural conditions for 24 hours.
PUM
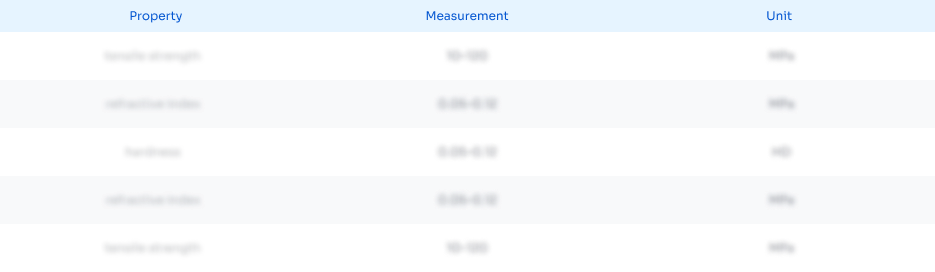
Abstract
Description
Claims
Application Information

- Generate Ideas
- Intellectual Property
- Life Sciences
- Materials
- Tech Scout
- Unparalleled Data Quality
- Higher Quality Content
- 60% Fewer Hallucinations
Browse by: Latest US Patents, China's latest patents, Technical Efficacy Thesaurus, Application Domain, Technology Topic, Popular Technical Reports.
© 2025 PatSnap. All rights reserved.Legal|Privacy policy|Modern Slavery Act Transparency Statement|Sitemap|About US| Contact US: help@patsnap.com