Dual-drive five-axis gantry machining center equipment and working method
A machining center, dual-drive technology, applied in metal processing equipment, metal processing mechanical parts, manufacturing tools, etc., can solve the problems of complex manufacturing and maintenance, affecting the machining accuracy and service life of machine tools, and increasing the load and wear of the third axis.
- Summary
- Abstract
- Description
- Claims
- Application Information
AI Technical Summary
Problems solved by technology
Method used
Image
Examples
Embodiment Construction
[0015] Such as Figure 1-4 As shown, this dual-drive five-axis gantry machining center equipment includes frame assembly I, electrical box assembly II, numerical control operating system III, first axis drive system IV, second axis drive system V, and third axis drive system VI, fourth axis drive system VII, fifth axis drive system VIII, head assembly IX, working platform assembly X;
[0016] The first shaft drive system is two first servo motors 1 distributed on both sides of the frame assembly, driving the first screw 2 to drive the first fixed frame 4 to perform reciprocating positioning motion in the X-axis direction; distributed on the first fixed frame 4 The two second servo motors 10 up and down drive the second screw rod 13 to drive the second fixed frame 11 to perform reciprocating positioning motion in the Y-axis direction; a third servo motor 9 distributed on the second fixed frame 11 drives the third The screw mandrel 8 drives the machine head assembly 6 to perfor...
PUM
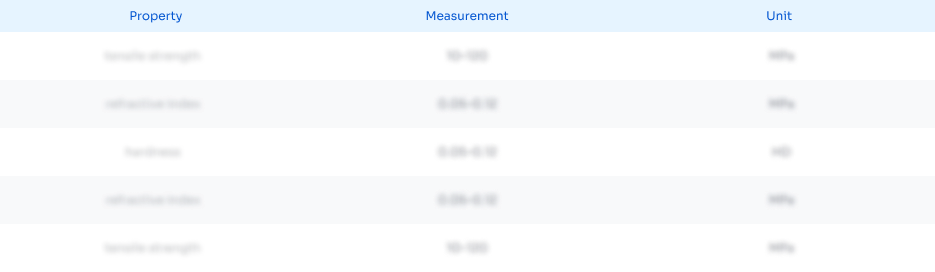
Abstract
Description
Claims
Application Information

- Generate Ideas
- Intellectual Property
- Life Sciences
- Materials
- Tech Scout
- Unparalleled Data Quality
- Higher Quality Content
- 60% Fewer Hallucinations
Browse by: Latest US Patents, China's latest patents, Technical Efficacy Thesaurus, Application Domain, Technology Topic, Popular Technical Reports.
© 2025 PatSnap. All rights reserved.Legal|Privacy policy|Modern Slavery Act Transparency Statement|Sitemap|About US| Contact US: help@patsnap.com