Multi-logistics robot collaborative path planning method based on task priority
A logistics robot and task priority technology, applied in the direction of instruments, motor vehicles, two-dimensional position/channel control, etc., can solve the problems of ignoring particularity, ignoring, and the existence of optimization space in the obtained path, so as to improve logistics efficiency and optimize The effect of planning paths and avoiding unnecessary detours
- Summary
- Abstract
- Description
- Claims
- Application Information
AI Technical Summary
Problems solved by technology
Method used
Image
Examples
Embodiment Construction
[0043] In order to make the technical problems, technical solutions and advantages to be solved by the present invention clearer, the following will describe in detail with reference to the drawings and specific embodiments.
[0044] Aiming at the existing problems, the present invention provides a multi-logistics robot collaborative path planning method based on task priority, such as figure 1 As shown, a kind of multi-logistics robot cooperative path planning method based on task priority of the present invention comprises the following steps:
[0045] Step S1, input the warehouse map and logistics task list: the warehouse map includes feasible paths, location nodes, static obstacles (such as walls, shelves, charging piles) and warehouse map storage map size information; the logistics task list includes the complete logistics of all tasks Demand, specifically including the timeliness level of the goods transported in each task, the AGV (Automated Guided Vehicle, automatic gu...
PUM
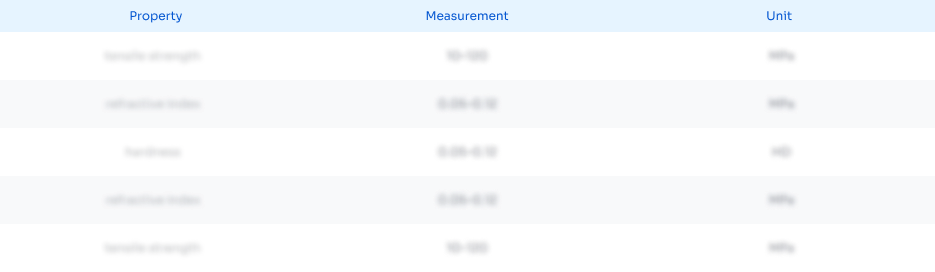
Abstract
Description
Claims
Application Information

- R&D Engineer
- R&D Manager
- IP Professional
- Industry Leading Data Capabilities
- Powerful AI technology
- Patent DNA Extraction
Browse by: Latest US Patents, China's latest patents, Technical Efficacy Thesaurus, Application Domain, Technology Topic, Popular Technical Reports.
© 2024 PatSnap. All rights reserved.Legal|Privacy policy|Modern Slavery Act Transparency Statement|Sitemap|About US| Contact US: help@patsnap.com