Friction stir welding tool and friction stir welding method
A technology of friction stir and welding methods, which is applied in the field of friction stir welding tools and friction stir welding, which can solve the problems of long length and impact on the durability of friction stir welding tools, and achieve buckling suppression, reduced operating costs, and improved durability Effect
- Summary
- Abstract
- Description
- Claims
- Application Information
AI Technical Summary
Problems solved by technology
Method used
Image
Examples
no. 1 Embodiment approach
[0025] Hereinafter, a tool for friction stir welding according to a first embodiment of the present invention will be described with reference to the drawings. exist figure 1 (a) shows a perspective view of the friction stir welding tool 100 according to the first embodiment viewed obliquely from above. figure 1 (b) shows the perspective view which looked at the tool 100 for friction stir welding which concerns on 1st Embodiment obliquely from below. exist figure 2 A side view of the tool 100 for friction stir welding is shown in . exist image 3 A cross-sectional view of the tool 100 for friction stir welding is shown in . image 3 is along figure 2 Sectional view of line III-III.
[0026] like Figure 1 ~ Figure 3 As shown, the friction stir welding tool 100 of this embodiment includes an upper shoulder (first shoulder portion) 10, a lower shoulder (second shoulder portion) 20, an intermediate shoulder (third shoulder portion) 30, and Agitator shaft 40. The middle...
no. 2 Embodiment approach
[0095] Next, a friction stir welding tool 100b according to a second embodiment of the present invention will be described. In addition, the description of the part which has the same structure as that of the said 1st Embodiment is abbreviate|omitted, and only a different part is demonstrated.
[0096] In the second embodiment, the opposing portion (first opposing portion) 35a facing the upper shoulder 10 via the upper slit x1 of the intermediate shoulder 30 and the lower platform via the lower slit x2 are configured. The opposing parts (second opposing parts) 35b facing the shoulders 20 can move relative to each other in the axial direction of the stirring shaft 40, and elastic bodies are arranged between the opposing parts. The implementation is different.
[0097] exist Figure 8 A side view of the tool 100b for friction stir welding in the second embodiment is shown in . exist Figure 8 (a) shows that the distance between the facing portion 35a facing the upper shoulde...
no. 3 Embodiment approach
[0104] Next, a friction stir welding tool 100c according to a third embodiment of the present invention will be described. In addition, the description of the part which has the same structure as the said 1st Embodiment and 2nd Embodiment is abbreviate|omitted, and only a different part is demonstrated.
[0105] In the third embodiment, the positions of the beam members w3 included in the workpieces W to be subjected to friction stir welding are different from those in the first and second embodiments. Along with this, the shape when viewed from the front of the intermediate shoulder 30 is different from the first embodiment and the second embodiment.
[0106] like Figure 4 As shown, in the first embodiment and the second embodiment, when the friction stir welding tool is viewed from the front, the cross section of the intermediate shoulder 30 along the mating direction D2 is a rectangular shape that is longer in the D2 direction. explained. In contrast, in the third embod...
PUM
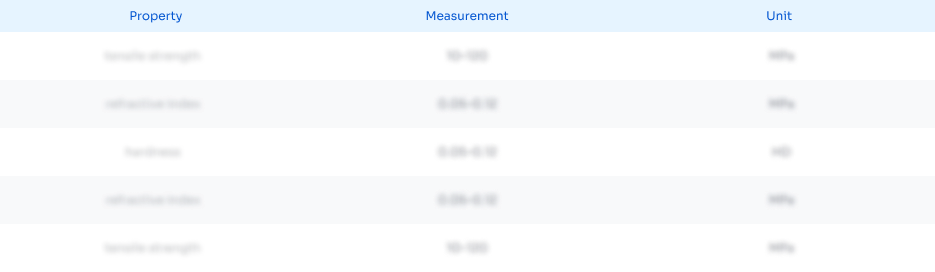
Abstract
Description
Claims
Application Information

- R&D
- Intellectual Property
- Life Sciences
- Materials
- Tech Scout
- Unparalleled Data Quality
- Higher Quality Content
- 60% Fewer Hallucinations
Browse by: Latest US Patents, China's latest patents, Technical Efficacy Thesaurus, Application Domain, Technology Topic, Popular Technical Reports.
© 2025 PatSnap. All rights reserved.Legal|Privacy policy|Modern Slavery Act Transparency Statement|Sitemap|About US| Contact US: help@patsnap.com