Low-eddy-current-loss primary structure of tooth groove type cylindrical linear motor
An eddy current loss, linear motor technology, applied in electrical components, electromechanical devices, electric components, etc., can solve the problems of inefficient use of electromagnetic energy, lack of primary yoke cores, and reduced thrust density, etc. quality, the effect of reducing voids
- Summary
- Abstract
- Description
- Claims
- Application Information
AI Technical Summary
Problems solved by technology
Method used
Image
Examples
Embodiment Construction
[0029] In this example, if figure 1 As shown, the primary structure of a cogging type cylindrical linear motor with low eddy current loss includes primary teeth 1, primary yoke 2 and multiple circular ring groups 3; wherein, primary teeth 1 and primary yoke 2 are separate components, And the primary yoke 2 is fitted on the outside of the primary tooth 1 and constitutes the primary iron core.
[0030] Such as figure 2 As shown, the primary tooth 1 includes a plurality of tooth core rings 4, and the scattered tooth core blocks 5 are clamped and positioned by two thin insulating plates 6, positioning pins 7 and positioning holes 8 to form a tooth core ring 4. One or more circular ring groups 3 are embedded between the two tooth core rings 4 . Both the tooth core rings 4 and the circular rings 3 are alternately clamped by two thin insulating plates 6 , and each circular ring 3 is located between the two tooth core rings 4 .
[0031] Such as image 3 As shown, the tooth core b...
PUM
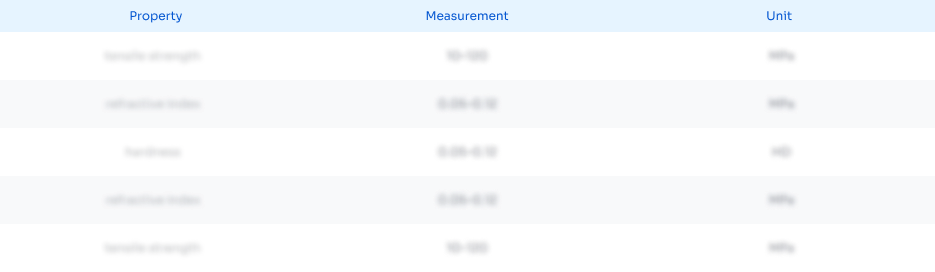
Abstract
Description
Claims
Application Information

- Generate Ideas
- Intellectual Property
- Life Sciences
- Materials
- Tech Scout
- Unparalleled Data Quality
- Higher Quality Content
- 60% Fewer Hallucinations
Browse by: Latest US Patents, China's latest patents, Technical Efficacy Thesaurus, Application Domain, Technology Topic, Popular Technical Reports.
© 2025 PatSnap. All rights reserved.Legal|Privacy policy|Modern Slavery Act Transparency Statement|Sitemap|About US| Contact US: help@patsnap.com