Teleoperation method for grasping operation of flying manipulator based on operator's intention recognition
A technology for operators and manipulators, applied in the field of grasping operation control of flying manipulators, can solve problems such as complex work environments, achieve the effects of improving control capabilities, ensuring precision, and enhancing the sense of presence
- Summary
- Abstract
- Description
- Claims
- Application Information
AI Technical Summary
Problems solved by technology
Method used
Image
Examples
Embodiment Construction
[0045] A remote operation method for grasping operation of a flying manipulator based on the operator's intention recognition is based on a system consisting of a master end, a slave end, and a communication link; Composed of machine interface, display and control computer, the slave end is the flying manipulator, and the communication link is wireless communication; the remote operation method includes the following steps:
[0046] Step 1. The control computer performs image processing on the on-site image sent back by the flying manipulator, and displays the image processing result of the operation scene on the monitor;
[0047] Step 2. When the operator looks at the display screen, the operator's eye movement characteristics are collected in real time through the eye tracking device to identify the operator's intention to grab the target, so as to lock the target;
[0048] Step 3. According to the recognition result of the operator's intention to grab the target, the UAV ap...
PUM
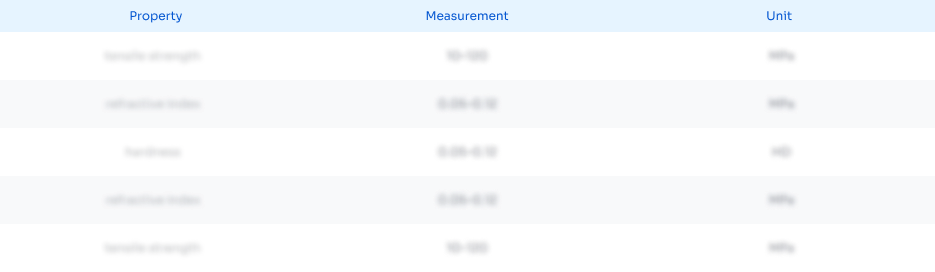
Abstract
Description
Claims
Application Information

- R&D
- Intellectual Property
- Life Sciences
- Materials
- Tech Scout
- Unparalleled Data Quality
- Higher Quality Content
- 60% Fewer Hallucinations
Browse by: Latest US Patents, China's latest patents, Technical Efficacy Thesaurus, Application Domain, Technology Topic, Popular Technical Reports.
© 2025 PatSnap. All rights reserved.Legal|Privacy policy|Modern Slavery Act Transparency Statement|Sitemap|About US| Contact US: help@patsnap.com