Line-driven continuous flexible mechanical arm and flexible robot comprising line-driven continuous flexible mechanical arm
A flexible robotic arm and continuous technology, applied in the field of flexible robots, can solve the problems of high sealing requirements, hysteresis, and bulky robot structure, and achieve the effect of precise control
- Summary
- Abstract
- Description
- Claims
- Application Information
AI Technical Summary
Problems solved by technology
Method used
Image
Examples
Embodiment
[0034] Such as figure 1 , 2, 3, 4, and 5, a line-driven continuous flexible manipulator includes a space flexible arm and a plurality of drive control modules 8 located at the top of the space flexible arm (the drive control module 8 is provided with four in this embodiment) 1), the space flexible arm comprises a plurality of flexible arm foldable skeletons 2 that are connected in series and arranged coaxially (in this embodiment, four flexible arm foldable skeletons 2 are arranged), the rigidity of the flexible arm foldable skeleton 2 can be The foldable skeleton is a 3D printed one-piece skeleton. The multiple flexible arm foldable skeletons 2 are all the same and have equal height dimensions. The flexible arm foldable skeleton 2 includes an upper platform 3, multiple bendable folding plates 4, and flexible springs 5 And lower platform 6, folding plate 4 and flexible spring 5 are all positioned between upper platform 3 and lower platform 6 and connect upper platform 3 and l...
PUM
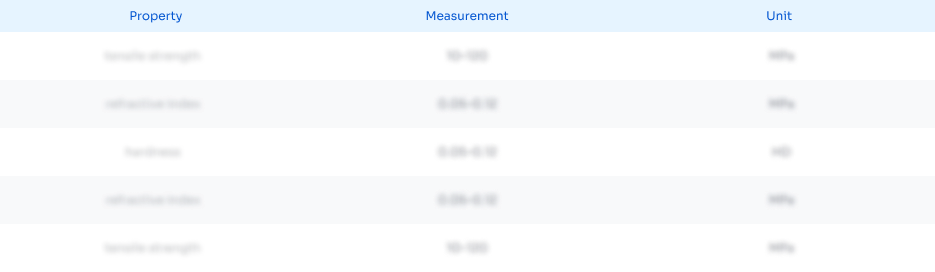
Abstract
Description
Claims
Application Information

- R&D
- Intellectual Property
- Life Sciences
- Materials
- Tech Scout
- Unparalleled Data Quality
- Higher Quality Content
- 60% Fewer Hallucinations
Browse by: Latest US Patents, China's latest patents, Technical Efficacy Thesaurus, Application Domain, Technology Topic, Popular Technical Reports.
© 2025 PatSnap. All rights reserved.Legal|Privacy policy|Modern Slavery Act Transparency Statement|Sitemap|About US| Contact US: help@patsnap.com