Gearbox state monitoring system
A state monitoring system and gearbox technology, applied in machine gear/transmission mechanism testing, electric components, electromechanical devices, etc., can solve the problems of magnetic interference, large additional space, small size, etc., and achieve high integration and reliability , strong power generation and power supply capabilities, and simple overall structure
- Summary
- Abstract
- Description
- Claims
- Application Information
AI Technical Summary
Problems solved by technology
Method used
Image
Examples
Embodiment Construction
[0019] The present invention proposes a gearbox state monitoring system, which mainly includes a fixed coil a, a moving coil b, a roller c, a bracket d, a left housing e, a right housing f, a left baffle g, a right baffle h; The body e and the right case f are installed on both sides of the fixed coil a through screws, the left baffle g and the right baffle h are installed on both sides of the moving coil b through screws, and both the left case e and the right case f are equipped with There is a fixed electrode ring i, a moving electrode ring j is provided on the left baffle g and the right baffle h, and a circuit board p and a sensor s are installed on the left shell e and the left baffle g; A group of passive magnets k, the rotating shaft Z is inlaid with an active magnet m, the number and installation radius of the active magnet m and the passive magnet k are the same, and the opposite magnetic poles are installed oppositely; the roller c is installed between the fixed coil...
PUM
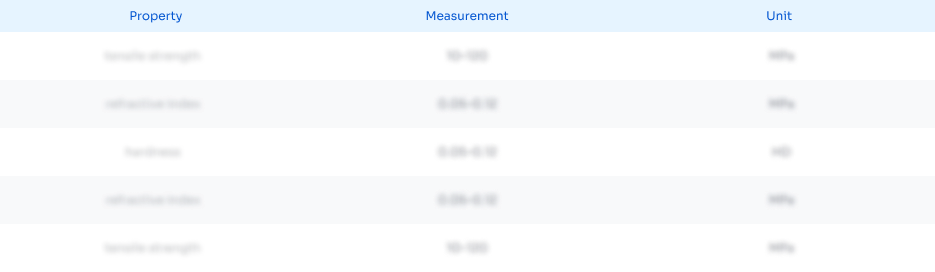
Abstract
Description
Claims
Application Information

- R&D Engineer
- R&D Manager
- IP Professional
- Industry Leading Data Capabilities
- Powerful AI technology
- Patent DNA Extraction
Browse by: Latest US Patents, China's latest patents, Technical Efficacy Thesaurus, Application Domain, Technology Topic, Popular Technical Reports.
© 2024 PatSnap. All rights reserved.Legal|Privacy policy|Modern Slavery Act Transparency Statement|Sitemap|About US| Contact US: help@patsnap.com