Belt filter press
A belt filter press, crawler technology, applied in the direction of filtration and separation, moving filter element filter, special treatment target, etc., can solve the problem of unsatisfactory treatment effect, etc., to alleviate the problem of sludge transportation and reuse water, easy maintenance, The effect of improving the dehydration effect
- Summary
- Abstract
- Description
- Claims
- Application Information
AI Technical Summary
Problems solved by technology
Method used
Image
Examples
Embodiment Construction
[0017] The present invention will be described in further detail below in conjunction with the accompanying drawings and specific embodiments. It should be understood that the specific embodiments described here are only used to explain the present invention, not to limit the present invention.
[0018] Such as figure 1 As shown, the belt filter press of the present invention includes an upper rotary crawler 1, a lower rotary crawler 2, and a pressure roller 3 rotatably arranged inside the upper rotary crawler. The outer wall of the pressure roller is provided with a plurality of The pressure blocks 4 extending radially and evenly spaced can contact the inner surface of the upper revolving track when the pressure roller 3 is driven to rotate and produce a pressing effect. The upper rotary track and the lower rotary track are arranged at intervals up and down, the upper rotary filter belt rotates counterclockwise under the drive of the upper rotary wheel 5, and the lower rotar...
PUM
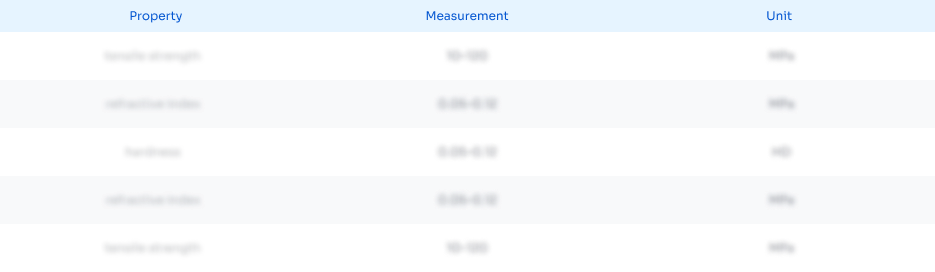
Abstract
Description
Claims
Application Information

- R&D
- Intellectual Property
- Life Sciences
- Materials
- Tech Scout
- Unparalleled Data Quality
- Higher Quality Content
- 60% Fewer Hallucinations
Browse by: Latest US Patents, China's latest patents, Technical Efficacy Thesaurus, Application Domain, Technology Topic, Popular Technical Reports.
© 2025 PatSnap. All rights reserved.Legal|Privacy policy|Modern Slavery Act Transparency Statement|Sitemap|About US| Contact US: help@patsnap.com