Normal sewing machine
A flat car and sewing technology, applied in the field of sewing, can solve the problems of fabric squeezing and wrinkling, uneven fabric thickness, affecting the smoothness of the fabric, etc., and achieve the effect of smooth fabric and overall smoothness of the fabric.
- Summary
- Abstract
- Description
- Claims
- Application Information
AI Technical Summary
Problems solved by technology
Method used
Image
Examples
Embodiment 1
[0028] Example 1: Please refer to Figure 1-Figure 5 , the specific embodiments of the present invention are as follows:
[0029] Its structure comprises a frame 1, a placement frame 2, a head 3, a workbench 4, an underframe 5, and a feeding structure 6. The placement frame 2 is vertically installed on the upper end of the frame 1 and is mechanically connected. The table 4 is horizontally installed on the upper end of the frame 1 and is fixedly connected, the machine head 3 is installed on the upper end of the workbench 4 and connected with each other, the bottom frame 5 is arranged on the right side of the frame 1, and the feeding structure 6 is installed horizontally At the upper end of the feeding structure 6 and mechanically connected, the upper left end of the feeding structure 6 communicates with the head 3 through a pipeline; the feeding structure 6 includes a cylinder 61, a gas pipe 62, a piston rod 63, a piston 64, and a conveying plate 65 The air pipe 62 is embedded...
Embodiment 2
[0035] Example 2: Please refer to Figure 5-Figure 8 , the specific embodiments of the present invention are as follows:
[0036] The adjustment roller 55b includes a rotating disk b1, a shaft hole b2, an outer ring b3, an adaptation groove b4, and a swing structure b5. The shaft hole b2 runs through the inside of the rotating disk b1 and is on the same axis. The outer ring b3 is installed on The outer side of the rotating disc b1 is fixedly connected, the adapting grooves b4 are recessed in the inner side of the outer ring b3 and evenly distributed, and the swing structure b5 is fixed on the outer side of the outer ring b3 and spaced between the adapting grooves b4.
[0037] refer to Figure 6 The swing structure b5 includes a fixed block b51, a rubber block b52, a rotating plate b53, and a rotating structure b54. The rubber block b52 is vertically installed on the lower end of the fixed block b51 and engaged with each other. The rotating plate b53 is installed on the fixed ...
PUM
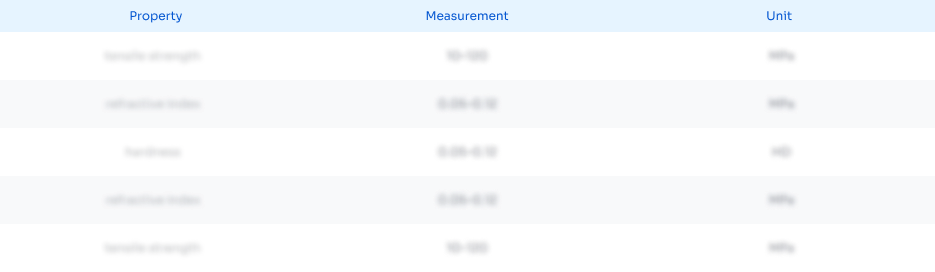
Abstract
Description
Claims
Application Information

- Generate Ideas
- Intellectual Property
- Life Sciences
- Materials
- Tech Scout
- Unparalleled Data Quality
- Higher Quality Content
- 60% Fewer Hallucinations
Browse by: Latest US Patents, China's latest patents, Technical Efficacy Thesaurus, Application Domain, Technology Topic, Popular Technical Reports.
© 2025 PatSnap. All rights reserved.Legal|Privacy policy|Modern Slavery Act Transparency Statement|Sitemap|About US| Contact US: help@patsnap.com