Sensor measuring point position determining method and device
A technology of measuring point location and determination method, which is applied in the direction of measuring devices, instruments, special data processing applications, etc., can solve the problem of sensor configuration redundancy and achieve the effect of avoiding redundancy
- Summary
- Abstract
- Description
- Claims
- Application Information
AI Technical Summary
Problems solved by technology
Method used
Image
Examples
Embodiment Construction
[0053]The embodiments will be described in detail hereinafter, examples of which are illustrated in the accompanying drawings. When the following description refers to the accompanying drawings, the same numerals in different drawings refer to the same or similar elements unless otherwise indicated. The implementations described in the following examples do not represent all implementations consistent with the examples of the present application. These are merely examples of systems and methods consistent with aspects of the embodiments of the present application as recited in the claims.
[0054] see figure 1 , figure 1 It is a flow chart of a method for determining the position of a sensor measuring point provided in an embodiment of the present application. Such as figure 1 shown, including the following steps:
[0055] Step 101, obtaining the strain mode matrix of the multi-order modes.
[0056] In step 101, the strain mode matrix of multi-order modes can be obtained...
PUM
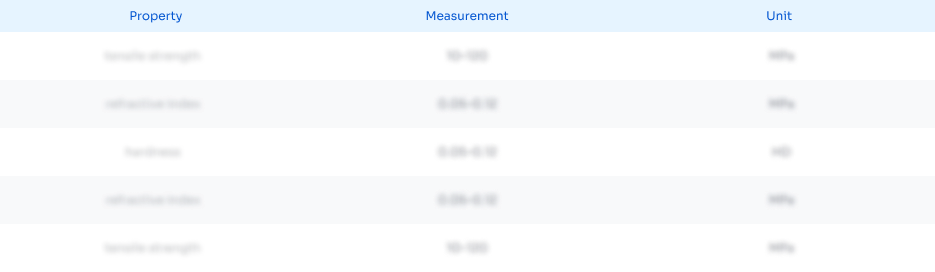
Abstract
Description
Claims
Application Information

- Generate Ideas
- Intellectual Property
- Life Sciences
- Materials
- Tech Scout
- Unparalleled Data Quality
- Higher Quality Content
- 60% Fewer Hallucinations
Browse by: Latest US Patents, China's latest patents, Technical Efficacy Thesaurus, Application Domain, Technology Topic, Popular Technical Reports.
© 2025 PatSnap. All rights reserved.Legal|Privacy policy|Modern Slavery Act Transparency Statement|Sitemap|About US| Contact US: help@patsnap.com