Numerically-controlled machine tool spindle unit static stiffness testing device and method
A technology of numerical control machine tools and testing devices, which is applied in the directions of measuring devices, testing of machine/structural components, testing of elasticity, etc., and can solve problems such as prone to error, unsatisfactory accuracy and practicability
- Summary
- Abstract
- Description
- Claims
- Application Information
AI Technical Summary
Problems solved by technology
Method used
Image
Examples
Embodiment Construction
[0035] The technical solution of this patent will be further described in detail below in conjunction with specific embodiments.
[0036] Such as Figure 1-8 As shown, the present invention provides a technical solution: a static stiffness testing device for the spindle unit of a CNC machine tool, including a bottom frame 1, the inner wall of the bottom frame 1 is overlapped with the outer surface of the moving frame 2, and the upper surface of the moving frame 2 is connected to the connecting block 3 The lower surface of the connecting block 3 is fixedly connected to the lower surface of the threaded cap 4. By setting the first motor 6, the threaded post 5, the threaded cap 4, the connecting block 3 and the moving frame 2, the first motor 6 can be Control threaded column 5 to rotate, and threaded column 5 controls threaded cap 4 and moving frame 2 to move to the left at the same time, can control force plate 152 to move to the left on the main shaft surface, guarantee the sta...
PUM
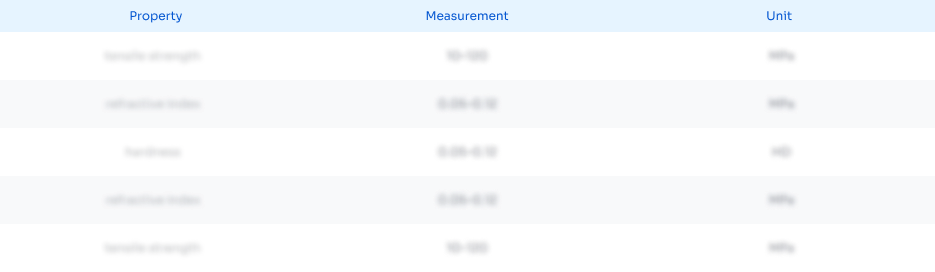
Abstract
Description
Claims
Application Information

- R&D
- Intellectual Property
- Life Sciences
- Materials
- Tech Scout
- Unparalleled Data Quality
- Higher Quality Content
- 60% Fewer Hallucinations
Browse by: Latest US Patents, China's latest patents, Technical Efficacy Thesaurus, Application Domain, Technology Topic, Popular Technical Reports.
© 2025 PatSnap. All rights reserved.Legal|Privacy policy|Modern Slavery Act Transparency Statement|Sitemap|About US| Contact US: help@patsnap.com