Alcohol-soluble flexographic inner printing ink suitable for extrusion composite process and preparation method thereof
An extrusion compounding and alcohol-soluble technology, which is applied in inks, applications, household appliances, etc., can solve problems such as difficult to meet market demand, poor ink transfer, high viscosity of flexographic printing inks, etc., to achieve market prospects and application value , good practicability and creativity, the effect of improving solubility and uniformity
- Summary
- Abstract
- Description
- Claims
- Application Information
AI Technical Summary
Problems solved by technology
Method used
Image
Examples
Embodiment 1
[0039] An alcohol-soluble flexographic printing ink suitable for extrusion compounding process, comprising the following components:
[0040] 21% alcohol-soluble nitrocellulose resin: 27.1%
[0041] 40% alcohol soluble polyurethane resin: 13%
[0042] Titanium dioxide: 40%
[0043] Polyethylene Wax: 0.5%
[0044] Fumed silica: 0.4%
[0045] Propylene Glycol Ethers: 4%
[0046] n-Propanol: 3%
[0047] Ethanol: 3%
[0048] 50% Modified Dammer Resin: 6%
[0049] Coupling agent: 3%.
[0050] A preparation method of alcohol-soluble flexographic printing ink suitable for extrusion compounding process, the specific steps are as follows:
[0051] S1. prepare a mixed solvent: accurately measure propylene glycol ethers, n-propanol and ethanol, add the two into a stirring tank, stir for 20min with a high-speed disperser at a stirring rate of 2000 r / min and fully mix, and take out part of the mixed solvent;
[0052] S2. Configure resin liquid: add alcohol-soluble nitrocellulose r...
Embodiment 2
[0057] An alcohol-soluble flexographic printing ink suitable for extrusion compounding process, comprising the following components:
[0058] 21% alcohol-soluble nitrocellulose resin: 25.1%
[0059] 40% alcohol soluble polyurethane resin: 13%
[0060] Organic Yellow Pigment: 15%
[0061] Polyethylene Wax: 0.5%
[0062] Fumed silica: 0.4%
[0063] Propylene Glycol Ethers: 13%
[0064] n-Propanol: 12%
[0065] Ethanol: 12%
[0066] 50% Modified Dammer Resin: 6%
[0067] Coupling agent: 3%.
[0068] 2. the alcohol-soluble flexographic printing ink suitable for extrusion compounding process according to claim 1, it is characterized in that: described alcohol-soluble nitrocellulose resin is set to 20-50% alcohol-soluble nitrocellulose resin solution .
[0069] A preparation method of alcohol-soluble flexographic printing ink suitable for extrusion compounding process, the specific steps are as follows:
[0070] S1. prepare a mixed solvent: accurately measure propylene glyco...
Embodiment 3
[0076] An alcohol-soluble flexographic printing ink suitable for extrusion compounding process, characterized in that it comprises the following components:
[0077] 21% alcohol-soluble nitrocellulose resin: 25.1%
[0078] 40% alcohol soluble polyurethane resin: 13%
[0079] Organic red pigment: 15%
[0080] Polyethylene Wax: 0.5%
[0081] Fumed silica: 0.4%
[0082] Propylene glycol ethers: 15%
[0083] n-Propanol: 12%
[0084] Ethanol: 10%
[0085] 50% Modified Dammer Resin: 6%
[0086] Coupling agent: 3%.
[0087] A preparation method of alcohol-soluble flexographic printing ink suitable for extrusion compounding process, the specific steps are as follows:
[0088] S1. prepare a mixed solvent: accurately measure propylene glycol ethers, n-propanol and ethanol, add the two into the stirring cylinder, stir for 35min with a high-speed disperser at a stirring rate of 1800 r / min and fully mix, and take out part of the mixed solvent;
[0089] S2. Configure resin liquid: ...
PUM
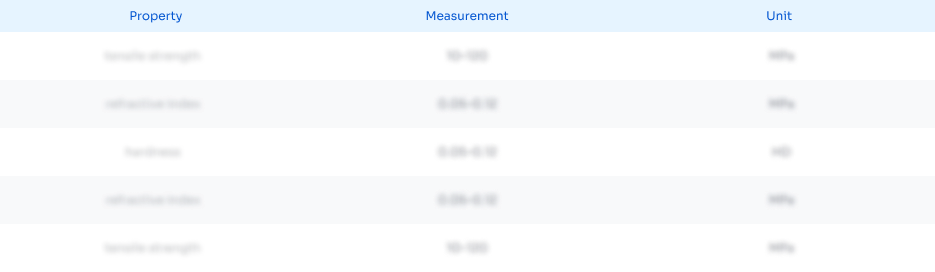
Abstract
Description
Claims
Application Information

- R&D Engineer
- R&D Manager
- IP Professional
- Industry Leading Data Capabilities
- Powerful AI technology
- Patent DNA Extraction
Browse by: Latest US Patents, China's latest patents, Technical Efficacy Thesaurus, Application Domain, Technology Topic, Popular Technical Reports.
© 2024 PatSnap. All rights reserved.Legal|Privacy policy|Modern Slavery Act Transparency Statement|Sitemap|About US| Contact US: help@patsnap.com