Double in-line package process
A dual-in-line packaging and process technology, which is applied in the direction of electrical components, inductors/transformers/magnets manufacturing, circuits, etc., can solve the problems of low yield rate, lead wire damage, and low yield rate of final finished products, so as to reduce paint removal temperature, avoid circuit damage, and ensure the effect of accuracy
- Summary
- Abstract
- Description
- Claims
- Application Information
AI Technical Summary
Problems solved by technology
Method used
Image
Examples
Embodiment Construction
[0032] In order to enable those skilled in the art to better understand the technical solutions of the present invention, the present invention will be further described in detail below in conjunction with specific embodiments.
[0033] Such as figure 1 As shown, a dual in-line packaging process is characterized in that it comprises the following steps:
[0034] Preliminary tinning, connect the wires of the network transformer 1 to the pins for preliminary tinning;
[0035] Preliminary baking, baking the network transformer 1 after preliminary tinning to prepare for the upper cover;
[0036] The upper cover is baked, and the network transformer 1 after the upper cover is baked to obtain a semi-finished product;
[0037] Secondary tinning, the semi-finished products after finishing and assembling the pins are subjected to secondary tinning of the assembling pins;
[0038] Finished product inspection, conduct high-voltage test and comprehensive test on semi-finished products ...
PUM
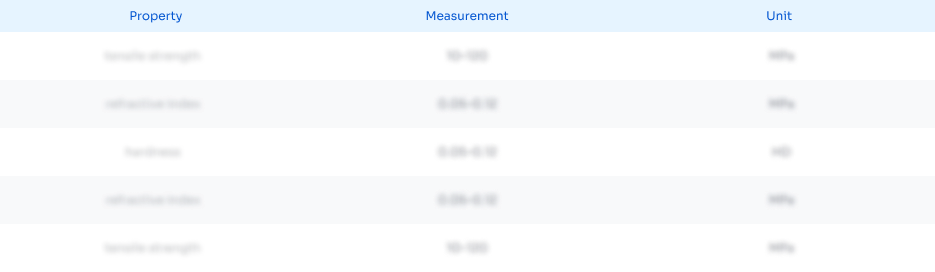
Abstract
Description
Claims
Application Information

- R&D
- Intellectual Property
- Life Sciences
- Materials
- Tech Scout
- Unparalleled Data Quality
- Higher Quality Content
- 60% Fewer Hallucinations
Browse by: Latest US Patents, China's latest patents, Technical Efficacy Thesaurus, Application Domain, Technology Topic, Popular Technical Reports.
© 2025 PatSnap. All rights reserved.Legal|Privacy policy|Modern Slavery Act Transparency Statement|Sitemap|About US| Contact US: help@patsnap.com