A binding device and its control method
A control method and equipment technology, applied in the direction of electrical components, electrical components, etc., can solve the problems of binding equipment affecting the binding accuracy, etc., and achieve the effects of reducing the average running time, reducing the internal vibration amplitude, and reducing the reaction force
- Summary
- Abstract
- Description
- Claims
- Application Information
AI Technical Summary
Problems solved by technology
Method used
Image
Examples
Embodiment 1
[0138]The basic scheme of the control method is: control the main motion platform to perform variable speed movement with the first acceleration relative to the first linear guide rail in the positioning step, and the direction of the first acceleration is always opposite to the direction of the second acceleration; wherein, the second Acceleration is the acceleration relative to the second linear guide when the working end is in the positioning step.
[0139] Since the first acceleration of the main motion platform is in the opposite direction to the second acceleration direction of the working end, during the positioning period, by controlling the main motion platform to perform a variable speed movement opposite to the acceleration direction of the working end, the working end and the working end The reaction force of the main motion platform acting on the inside of the binding device is in the opposite direction, that is, the reaction force of the main motion platform can b...
Embodiment 2
[0156] Since the overall mass of the working end is smaller than that of the main motion platform, in order to simplify the control scheme, the influence of the working end on the vibration amplitude inside the binding device can be ignored. At this point, the control method is:
[0157] The main motion platform is controlled to move at a constant speed at a first preset speed on the first linear guide rail in the first binding step, the positioning step and the second binding step. The working end moves at a constant speed at a second preset speed during the first binding step and the second binding step.
[0158] Compared with the technical solution in which the main motion platform and the working end perform variable speed movement in the first positioning step and the second positioning step, the technical solution of this embodiment can simplify the control procedure of the binding equipment, and is more conducive to the control of the binding equipment . It should be ...
Embodiment 3
[0173] In order to further reduce the vibration amplitude caused by the reaction force generated during the reciprocating movement of the working end inside the binding device, the main motion platform is controlled on the first linear guide rail in the first binding step, positioning step, and second binding step. On the basis of performing uniform motion at the first preset speed, the binding device also includes:
[0174] The reciprocating end is arranged on the second linear guide rail.
[0175] The third driving device is used to drive the reciprocating end to move on the second linear guide rail, and the control device is also connected to the third driving device.
[0176] At this time, the positioning step further includes: controlling the reciprocating end to reciprocate on the second linear guide rail at a third acceleration, and making the direction of the third acceleration always opposite to the direction of the second acceleration.
[0177] Since the direction o...
PUM
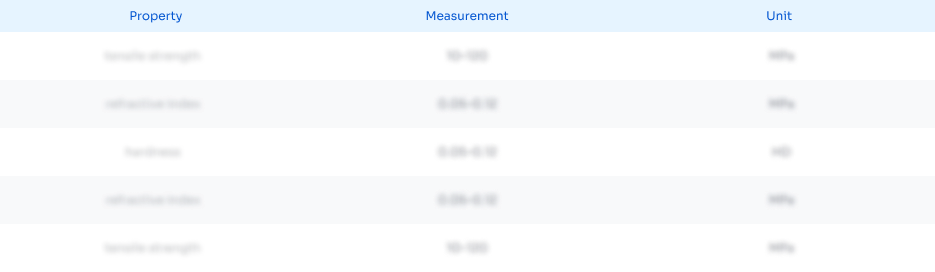
Abstract
Description
Claims
Application Information

- R&D Engineer
- R&D Manager
- IP Professional
- Industry Leading Data Capabilities
- Powerful AI technology
- Patent DNA Extraction
Browse by: Latest US Patents, China's latest patents, Technical Efficacy Thesaurus, Application Domain, Technology Topic, Popular Technical Reports.
© 2024 PatSnap. All rights reserved.Legal|Privacy policy|Modern Slavery Act Transparency Statement|Sitemap|About US| Contact US: help@patsnap.com