Overall airtightness detection method for pressure vessel
A technology for air tightness testing and pressure vessels, which is applied in liquid tightness measurement using liquid/vacuum degree, testing of machine/structural components, fluid tightness testing, etc. , time-consuming problems in the test process, etc., to achieve accurate and reliable judgment results, save the cost of measuring devices and measurement time, and make the measuring devices and implementation steps simple and common.
- Summary
- Abstract
- Description
- Claims
- Application Information
AI Technical Summary
Problems solved by technology
Method used
Image
Examples
Embodiment 1
[0046] When the pressure vessel can be equipped with a temperature detection point, combined with figure 1 and figure 2 As shown, as a specific embodiment of the present invention, a method for detecting the overall airtightness of a pressure vessel includes:
[0047] Through the pressure gauge and thermocouple, obtain the time t of the pressure vessel at the completion of the boost max The corresponding maximum pressure value p max and the maximum temperature T max ;
[0048] According to the maximum pressure value p max and the maximum temperature T max , use the Refprop9.0_NIST physical property query software to determine the gas density ρ in the pressure vessel g , that is, ρ g =f(p max ,T max );
[0049] Through the pressure gauge and thermocouple, obtain the pressure vessel at the detection time t 1 Corresponding actual pressure value p 1 and the actual temperature value T 1 ;
[0050] According to the gas density ρ g and the actual temperature value T ...
Embodiment 2
[0054] When the pressure vessel cannot be equipped with temperature measuring points, first assume that the pressure vessel has good airtightness, and obtain the change law of pressure with time according to the pressure measurement data at different times, and obtain the theory at any time according to the change law of pressure with time Finally, compare the theoretical pressure value with the actual pressure measurement value of the detection point to verify the airtightness of the pressure vessel, as follows:
[0055] to combine figure 1 and image 3 As shown, as a specific embodiment of the present invention, a method for detecting the overall airtightness of a pressure vessel includes:
[0056] Through the pressure gauge, obtain the boosting completion time t of the pressure vessel max and at the boost completion time t max The corresponding maximum pressure value p max .
[0057] Obtain the first moment t of the pressure vessel during the pressure holding process t...
PUM
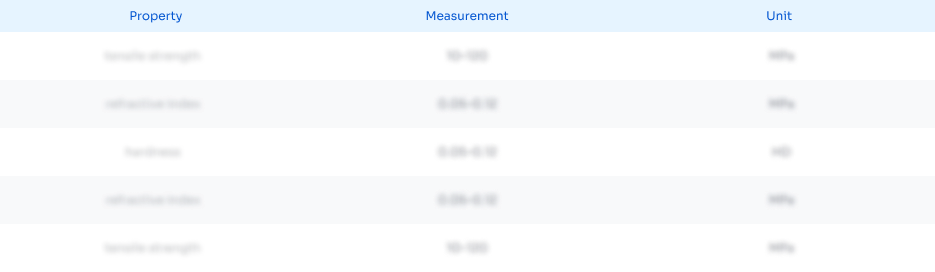
Abstract
Description
Claims
Application Information

- R&D Engineer
- R&D Manager
- IP Professional
- Industry Leading Data Capabilities
- Powerful AI technology
- Patent DNA Extraction
Browse by: Latest US Patents, China's latest patents, Technical Efficacy Thesaurus, Application Domain, Technology Topic, Popular Technical Reports.
© 2024 PatSnap. All rights reserved.Legal|Privacy policy|Modern Slavery Act Transparency Statement|Sitemap|About US| Contact US: help@patsnap.com