Movement mechanism applied to low-temperature vacuum environment
A motion mechanism and low-temperature vacuum technology, which is applied to packaging, heat preservation, and mechanical equipment under vacuum/special atmosphere, can solve problems such as motion mechanism jamming, and achieve the effect of improving the use effect and reducing the jamming phenomenon
- Summary
- Abstract
- Description
- Claims
- Application Information
AI Technical Summary
Problems solved by technology
Method used
Image
Examples
Embodiment Construction
[0025] The following will clearly and completely describe the technical solutions in the embodiments of the present invention with reference to the drawings in the embodiments of the present invention.
[0026] Such as Figure 1-5 As shown, the motion mechanism applied to a low-temperature vacuum environment of the present invention may include a vacuum container 1, a driving assembly 2, a cold plate 3, a driven assembly 4, a driving mechanism insulation 5 and a driven mechanism insulation 6, and the cold plate The two ends of 3 are respectively connected with the driving assembly 2 and the driven assembly 4, and the driving mechanism insulation 5 is arranged on the driving assembly 2, so that the driving assembly 2 maintains a certain temperature, and the driven mechanism insulation 6 is arranged on the driven assembly 4 so that the driven assembly 4 maintains a certain temperature; the driving assembly 2 and the driven assembly 4 are respectively fixed on the inner wall of t...
PUM
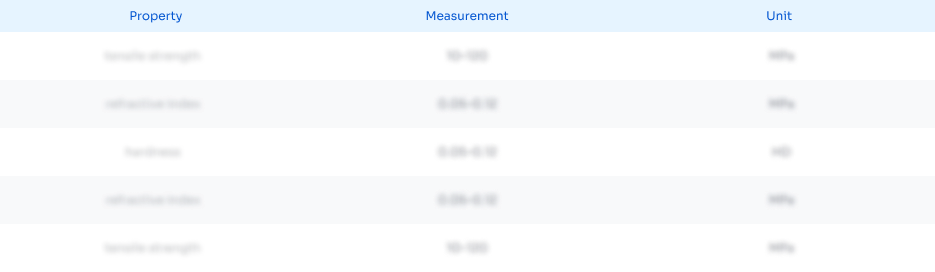
Abstract
Description
Claims
Application Information

- R&D Engineer
- R&D Manager
- IP Professional
- Industry Leading Data Capabilities
- Powerful AI technology
- Patent DNA Extraction
Browse by: Latest US Patents, China's latest patents, Technical Efficacy Thesaurus, Application Domain, Technology Topic, Popular Technical Reports.
© 2024 PatSnap. All rights reserved.Legal|Privacy policy|Modern Slavery Act Transparency Statement|Sitemap|About US| Contact US: help@patsnap.com