Forging process of inner straight hole part
A process, straight hole technology, applied in the field of forging, can solve the problems of decreased production efficiency, affected inner surface strength of the hole, increased production cost, etc., to achieve the effect of improving accuracy, avoiding disordered flow, and reducing machining cost.
- Summary
- Abstract
- Description
- Claims
- Application Information
AI Technical Summary
Problems solved by technology
Method used
Image
Examples
Embodiment 1
[0025] A forging process for inner straight hole parts, comprising the following steps:
[0026] (S1) Accurately weigh the metal blank, heat it at a heating rate of 170 °C / h to 1105 °C and roll it into a ring shape, then heat it again at a heating rate of 130 °C / h to 1180 °C and hold it for 120 minutes.
[0027] (S2) Put the reheated annular metal blank obtained in step (S1) into a forging die preheated to 295° C. for forging; wherein, the forging die includes a forming lower die, a forming upper die and a punch; forming The center of the lower die is provided with a counterbore that can accommodate the punch, and the center of the forming upper die is provided with a vertical pipe hole for the punch to pass through; when forging, the ring-shaped metal blank is placed horizontally on the forming lower die, and the punch first falls into the The counterbore occupies the central position, and then the forming upper die falls to forge the ring-shaped metal blank; after the forgin...
Embodiment 2
[0040] A forging process for inner straight hole parts, comprising the following steps:
[0041] (S1) Accurately weigh the metal blank, heat it at a heating rate of 160 °C / h to 1080 °C and roll it into a ring shape, then heat it again at a heating rate of 120 °C / h to 1170 °C and keep it for 60 minutes.
[0042] (S2) Put the twice-heated annular metal blank obtained in step (S1) into a forging die preheated to 290°C for forging; wherein, the forging die includes a forming lower die, a forming upper die and a punch; forming The center of the lower die is provided with a counterbore that can accommodate the punch, and the center of the forming upper die is provided with a vertical pipe hole for the punch to pass through; when forging, the ring-shaped metal blank is placed horizontally on the forming lower die, and the punch first falls into the The counterbore occupies the central position, and then the forming upper die falls to forge the ring-shaped metal blank; after the forgi...
Embodiment 3
[0055] A forging process for inner straight hole parts, comprising the following steps:
[0056] (S1) Accurately weigh the metal blank, heat it at a heating rate of 180 °C / h to 1120 °C and roll it into a ring shape, then heat it again at a heating rate of 130 °C / h to 1190 °C and hold it for 180 min.
[0057] (S2) Put the reheated annular metal blank obtained in step (S1) into a forging die preheated to 320° C. for forging; wherein, the forging die includes a forming lower die, a forming upper die and a punch; forming The center of the lower die is provided with a counterbore that can accommodate the punch, and the center of the forming upper die is provided with a vertical pipe hole for the punch to pass through; when forging, the ring-shaped metal blank is placed horizontally on the forming lower die, and the punch first falls into the The counterbore occupies the central position, and then the forming upper die falls to forge the ring-shaped metal blank; after the forging is...
PUM
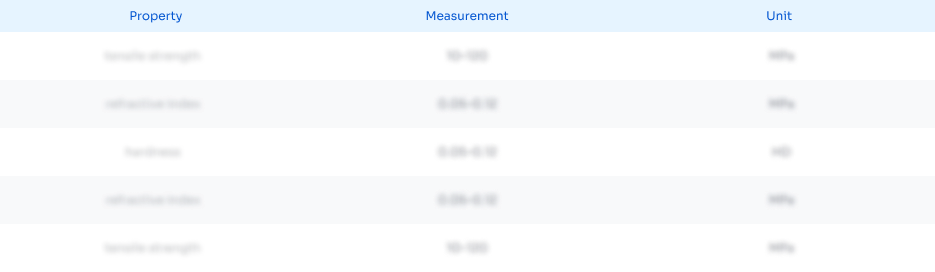
Abstract
Description
Claims
Application Information

- R&D
- Intellectual Property
- Life Sciences
- Materials
- Tech Scout
- Unparalleled Data Quality
- Higher Quality Content
- 60% Fewer Hallucinations
Browse by: Latest US Patents, China's latest patents, Technical Efficacy Thesaurus, Application Domain, Technology Topic, Popular Technical Reports.
© 2025 PatSnap. All rights reserved.Legal|Privacy policy|Modern Slavery Act Transparency Statement|Sitemap|About US| Contact US: help@patsnap.com