Small aviation piston engine crankshaft butt joint measuring device
A piston engine and measuring device technology, applied in the direction of measuring devices, optical devices, instruments, etc., can solve the problems of repeated calibration process, inability to quantify control and adjustment, and cumbersome measurement process, so as to eliminate the deviation of the measurement system and improve the docking accuracy , Eliminate the effect of system drift
- Summary
- Abstract
- Description
- Claims
- Application Information
AI Technical Summary
Problems solved by technology
Method used
Image
Examples
Embodiment Construction
[0026] This embodiment is a small aviation piston engine crankshaft joint measuring device.
[0027] refer to Figure 1 ~ Figure 4 , the present embodiment small aviation piston engine crankshaft docking measuring device, by positioning docking tooling 1, left section locator 2, middle section locator 3, right section locator 4, sliding guide rail 5, lead screw 6, driving motor 7, crankshaft parts 8. Measuring head 9, calibration part 10, host computer 11, data acquisition module 12, model generation module 13, and data analysis module 14; among them, the positioning docking tool 1 is used as the actuator, which is divided into the left locator 2 and the middle positioning The device 3 and the right section locator 4 are installed on the positioning and docking tool 1 by the docked measuring crankshaft component 8 . The middle section locator 3 and the right section locator 4 are installed on two parallel sliding guide rails 5, and the sliding guide rails 5 are fixedly connec...
PUM
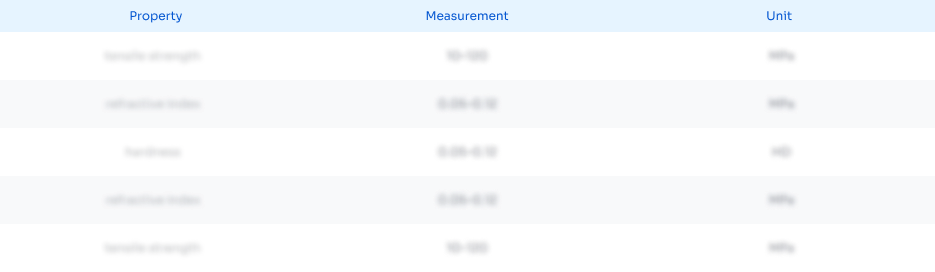
Abstract
Description
Claims
Application Information

- R&D
- Intellectual Property
- Life Sciences
- Materials
- Tech Scout
- Unparalleled Data Quality
- Higher Quality Content
- 60% Fewer Hallucinations
Browse by: Latest US Patents, China's latest patents, Technical Efficacy Thesaurus, Application Domain, Technology Topic, Popular Technical Reports.
© 2025 PatSnap. All rights reserved.Legal|Privacy policy|Modern Slavery Act Transparency Statement|Sitemap|About US| Contact US: help@patsnap.com