Cobalt-coated ceramic composite powder and preparation method and application thereof
A technology of ceramic composite and ceramic powder, applied in the directions of additive manufacturing, transportation and packaging, metal processing equipment, etc., can solve the problems of reducing the mechanical properties of formed parts, affecting the interface bonding strength, peeling off the surface ceramic layer, etc., to reduce the thermal expansion coefficient, It is not easy to break and agglomerate, and the effect of high interface bonding strength
- Summary
- Abstract
- Description
- Claims
- Application Information
AI Technical Summary
Benefits of technology
Problems solved by technology
Method used
Image
Examples
Embodiment 1
[0048] 2.5 g of cobalt acetate tetrahydrate was dissolved in 18 ml of absolute ethanol to obtain a homogeneously dispersed lyosol.
[0049] Add 3.4g Al to the lyosol 2 o 3 powder and 15ml of butyric acid solution with a concentration of 0.05mol / L, and magnetically stirred to obtain Al 2 o 3 A homogeneous suspension of ceramic powder.
[0050] 1.7 g of oxalic acid was dissolved in 17 ml of absolute ethanol to obtain an oxalic acid ethanol solution with an oxalate ion concentration of 0.8 mol / L.
[0051] At room temperature, add the above-mentioned oxalic acid ethanol solution to the suspension, and maintain it for 40 minutes under mechanical stirring at a rotational speed of 500r / min. After the reaction is completed, centrifuge, wash with deionized water for 3 times, wash with absolute ethanol for 2 times, and dry , to obtain the coated ceramic particle precursor powder.
[0052] Put the obtained coated ceramic particle precursor powder into a tube furnace, feed a mixture ...
Embodiment 2
[0060] 6 g of cobalt chloride was dissolved in 42 ml of anhydrous ether to obtain a homogeneously dispersed lyosol.
[0061] Add 8.5g ZrO to the lyosol 2 Powder and 30ml concentration of 0.05mol / L valeric acid solution, magnetic stirring, to obtain ZrO 2 A homogeneous suspension of ceramic powder.
[0062] 4.7 g of sodium oxalate was dissolved in 44 ml of anhydrous ether to obtain an oxalate ether solution with an oxalate ion concentration of 0.8 mol / L.
[0063] At room temperature, add the above-mentioned ethyl oxalate solution into the suspension, and maintain it for 50 minutes under mechanical stirring at a speed of 500 r / min. After the reaction is completed, centrifuge, wash with deionized water for 3 times, wash with absolute ethanol for 2 times, and dry , to obtain the coated ceramic particle precursor powder.
[0064] Put the obtained coated ceramic particle precursor powder into a tube furnace, feed a mixture of hydrogen and argon as a reducing gas, and heat up to 5...
Embodiment 3
[0067] Dissolve 5.8 g of cobalt nitrate in 34 ml of anhydrous methanol to obtain a homogeneously dispersed lyosol.
[0068] 6.8 g of SiC powder and 18 ml of capric acid solution with a concentration of 0.05 mol / L were added to the lyosol, and magnetically stirred to obtain a homogeneously dispersed suspension of SiC ceramic powder.
[0069] 2.96g of sodium carbonate was dissolved in 35ml of anhydrous methanol to obtain a sodium carbonate methanol solution with a carbonate ion concentration of 0.8mol / L.
[0070] At normal temperature, the above-mentioned sodium carbonate methanol solution was added to the suspension, maintained at a speed of 500r / min under mechanical stirring for 50min, after the reaction was completed, centrifuged, washed 3 times with deionized water and 2 times with absolute ethanol, Dry to obtain the coated ceramic particle precursor powder.
[0071] The obtained coated ceramic particle precursor powder was put into a tube furnace, and a mixed gas of hydrog...
PUM
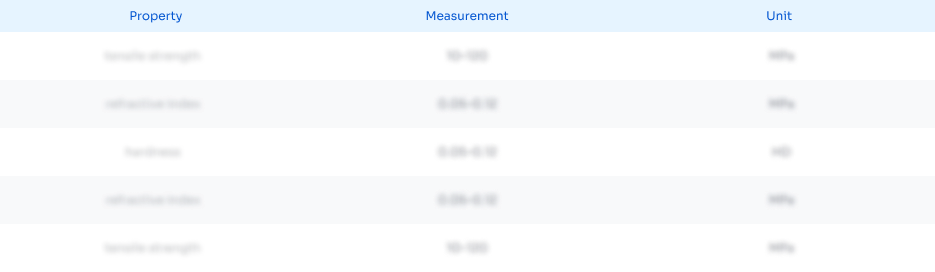
Abstract
Description
Claims
Application Information

- R&D
- Intellectual Property
- Life Sciences
- Materials
- Tech Scout
- Unparalleled Data Quality
- Higher Quality Content
- 60% Fewer Hallucinations
Browse by: Latest US Patents, China's latest patents, Technical Efficacy Thesaurus, Application Domain, Technology Topic, Popular Technical Reports.
© 2025 PatSnap. All rights reserved.Legal|Privacy policy|Modern Slavery Act Transparency Statement|Sitemap|About US| Contact US: help@patsnap.com