Manufacturing method of driver fence rear enclosure and manufacturing method of driver fence driver door
A production method and driver door technology, which are applied in the field of passenger car interior parts, can solve the problems of long production cycle, complex construction procedures, long construction time, etc., and achieve the effects of good batch consistency, simple overall structure and high assembly efficiency.
- Summary
- Abstract
- Description
- Claims
- Application Information
AI Technical Summary
Problems solved by technology
Method used
Image
Examples
example 1
[0041] Example 1: Surrounded by bus drivers
[0042] The bus driver is surrounded by the driver's rear enclosure 1, surrounding door 2, rear windshield glass 7, installation profile 8 (rotating shaft profile), installation profile 9 (side glass fixing profile), hinge 10, side barrier glass 11 and installation profile 12 (side glass fixing profiles) assembled. The rear enclosure 1 and the enclosure door 2 are processed by integral foam molding,
[0043] The production of the driver’s enclosure rear enclosure: 1) Preparation of the rear enclosure foaming mold, the preparation of the rear enclosure foaming mold, the metal mold 13 is used, and according to the shape and structure requirements of the rear enclosure 1, it is divided into rear enclosures in the lower mold 3. The lower part 1a of the back wall, the top reinforcing belt 1b of the back wall, the cuttable part 1c of the back wall, the sunken platform 7a installed on the back glass, the outer surface material leather 1-1...
PUM
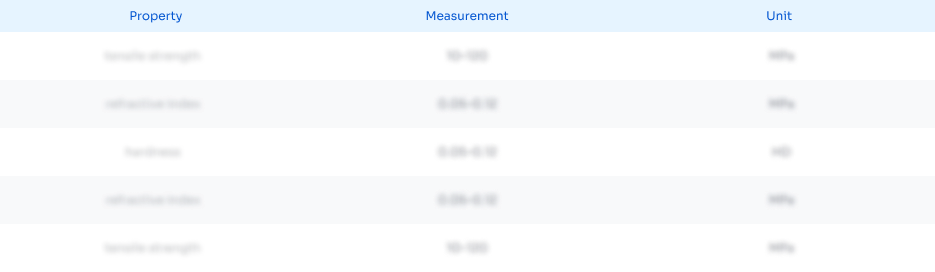
Abstract
Description
Claims
Application Information

- R&D Engineer
- R&D Manager
- IP Professional
- Industry Leading Data Capabilities
- Powerful AI technology
- Patent DNA Extraction
Browse by: Latest US Patents, China's latest patents, Technical Efficacy Thesaurus, Application Domain, Technology Topic, Popular Technical Reports.
© 2024 PatSnap. All rights reserved.Legal|Privacy policy|Modern Slavery Act Transparency Statement|Sitemap|About US| Contact US: help@patsnap.com