Patch pressurizing device and method for sensor
A pressurizing device and sensor technology, applied in the field of sensors, can solve problems such as low qualification rate and uneven pressurization force, and achieve the effect of improving productivity
- Summary
- Abstract
- Description
- Claims
- Application Information
AI Technical Summary
Problems solved by technology
Method used
Image
Examples
Embodiment 1
[0039] A patch pressure device for a sensor, comprising a positioning plate 10, a polytetrafluoroethylene plastic film 3, a pressure transmission plate 4, a spring 6, a fixed base 8, a guide rod 7, a nut 11, a buffer pad 4 and an adhesive tape 9. When in use, tighten the guide rod 7 on the fixed base 8, and place the spring 6, the pressure transmission plate, the buffer pad 4, the polytetrafluoroethylene film 3, and the positioning plate upwards in sequence according to the assembly relationship. The sensor 1 that has been pasted has been placed on the positioning plate. 10), the nut parts, then apply the rated pressurization force, after the pressurization is completed, lock the nut 11, and finally remove the rated pressurization force, the patch area 15 of the sensor 1 can be completed for patch pressurization.
[0040] The parts of the fixed base 8 include a threaded hole 13 for fixing the guide rod 7, and a step hole for placing the spring 6 concentrically with the threaded...
Embodiment 2
[0051] In order to solve the problem that the sensor is not easy to locate in the pressurization process of the micro-sensor patch, and the patch pressure is uneven, resulting in uneven adhesive layer after curing, air bubbles, and low process qualification rate caused by lack of glue, the present invention provides a sensor. Tablet pressing device, such as figure 1 , figure 2 with image 3 As shown, as a specific embodiment of the present invention, a sensor patch pressing device includes a pressure transmission plate 5 , a high temperature compression spring 6 , a guide rod 7 , a fixed base 8 , a positioning plate 10 and a wing nut 11 . The lower end of the guide rod 7 is threaded, and is screwed into the threaded hole 13 on the fixing seat 8, thereby establishing the guide rod reference;
[0052] A spring 6 is placed on the guide rod 7, the lower end of the spring 6 is placed in the spring counterbore 12 on the fixed base 7, the upper end of the spring 6 is in contact wi...
PUM
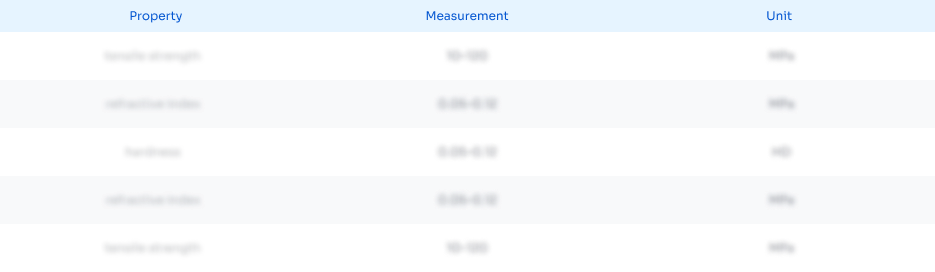
Abstract
Description
Claims
Application Information

- R&D
- Intellectual Property
- Life Sciences
- Materials
- Tech Scout
- Unparalleled Data Quality
- Higher Quality Content
- 60% Fewer Hallucinations
Browse by: Latest US Patents, China's latest patents, Technical Efficacy Thesaurus, Application Domain, Technology Topic, Popular Technical Reports.
© 2025 PatSnap. All rights reserved.Legal|Privacy policy|Modern Slavery Act Transparency Statement|Sitemap|About US| Contact US: help@patsnap.com