Cast-in-place mold for building bridge stand column pouring
A bridge and column technology, applied in the field of cast-in-place molds, can solve problems such as mold punctures, safety hazards, support failures, etc., and achieve the effects of uniform contact force, avoiding damage, and more contact points
- Summary
- Abstract
- Description
- Claims
- Application Information
AI Technical Summary
Problems solved by technology
Method used
Image
Examples
Embodiment 1
[0032] A cast-in-situ mold for building bridge columns, including two templates 1 that can be spliced and assembled. The template 1 is made of Q235 ordinary carbon structural steel plate with a wall thickness of 16mm; before pouring, it is necessary to paint the inside of the template 1 with an oil film , or covered by a plastic film, to facilitate demoulding in the later stage; two templates 1 are combined to form a mold cavity 101 for pouring concrete, and an arc-shaped reinforcing plate 2 is welded at the outer wall of the template 1, and the reinforcing plate 2 The two ends of the ear plates 201 are bent to form ear plates 201, and bolts 202 are installed between the two ear plates 201. After the bolts 202 are tightened, the assembly of the two templates 1 is completed; block; a plurality of arc-shaped positioning grooves 203 are distributed circularly on the outer side of the reinforcing plate 2, and on the outer side of the template 1, a plurality of vertical rods 204 a...
Embodiment 2
[0034] After the two modules 1 are spliced together, a V-shaped card slot is formed at the joint position, and a rubber sealing strip 6 is arranged in the V-shaped card slot formed by the combination, and the sealing strip 6 is squeezed and deformed; the above The structure can avoid leakage when pouring concrete.
Embodiment 3
[0036] A steel cable 7 is assembled between the exteriors of a plurality of said vertical rods 204, and said steel cable 7 is helically wound on the exteriors of a plurality of said vertical rods 204; Ribs 221 are arranged between the plates 2; the steel cables 7 can apply a tightening force between a plurality of vertical rods 204, and form a whole with the vertical rods 204 that originally apply external pressure on the outside alone, and apply a whole The force of adduction avoids expansion and leakage at the joint position of the formwork.
PUM
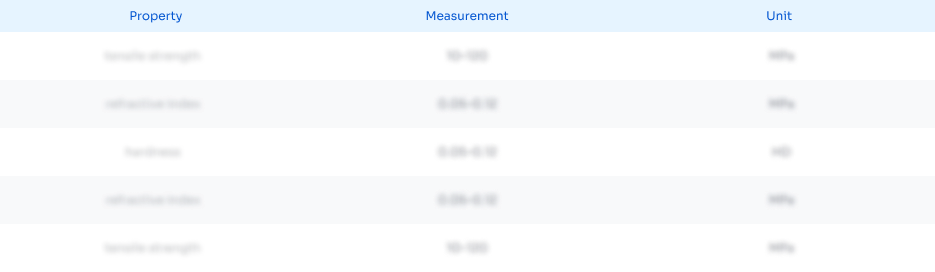
Abstract
Description
Claims
Application Information

- R&D
- Intellectual Property
- Life Sciences
- Materials
- Tech Scout
- Unparalleled Data Quality
- Higher Quality Content
- 60% Fewer Hallucinations
Browse by: Latest US Patents, China's latest patents, Technical Efficacy Thesaurus, Application Domain, Technology Topic, Popular Technical Reports.
© 2025 PatSnap. All rights reserved.Legal|Privacy policy|Modern Slavery Act Transparency Statement|Sitemap|About US| Contact US: help@patsnap.com