High temperature and high pressure resistant perforated plug and preparation method thereof
A perforated plug and high temperature resistant technology, which is applied in the manufacture of tools, metal rolling, metal rolling, etc., can solve the problems of wear resistance and high temperature resistance, cracking, flat nose and other problems, and achieve excellent heat resistance and improve High temperature and pressure resistance, life-enhancing effects
- Summary
- Abstract
- Description
- Claims
- Application Information
AI Technical Summary
Problems solved by technology
Method used
Image
Examples
Embodiment 1
[0030] According to the composition elements and mass percentages of perforated plugs described in Table 1, Example 1, the raw materials are prepared, and the raw materials are smelted, refined, poured, processed and formed; the processed and formed plugs are machined, and phosphorus is formed on the surface of the plugs with a phosphating solution. For the chemical film, the mass percentage of the phosphating solution is as follows: 22% phosphoric acid, 6% zinc oxide, 9% manganese nitrate, 10% dodecanol, and the balance is water. Then heat the plug to 910°C for annealing, keep it warm for 2 hours, then take it out of the furnace to cool at 320°C, and perform ZrN coating treatment on the coating machine to obtain the finished perforated plug. The target voltage of the coating machine is 450V, and the target power is 25W / CM 2 , the pulse bias voltage is 180V, the duty cycle is 80%, and the coating time is 25min.
Embodiment 2
[0032] According to the composition elements and mass percentages of perforated plugs described in Table 1, Example 2, the raw materials are prepared, and the raw materials are smelted, refined, poured, processed and formed; the processed and formed plugs are machined, and phosphorus is formed on the surface of the plugs with a phosphating solution. For the chemical film, the mass percentage of the phosphating solution is as follows: 22% phosphoric acid, 6% zinc oxide, 9% manganese nitrate, 10% dodecanol, and the balance is water. Then heat the plug to 910°C for annealing, keep it warm for 2 hours, then take it out of the furnace to cool at 320°C, and perform ZrN coating treatment on the coating machine to obtain the finished perforated plug. The target voltage of the coating machine is 450V, and the target power is 25W / CM 2 , the pulse bias voltage is 180V, the duty cycle is 80%, and the coating time is 25min.
Embodiment 3
[0034] Prepare raw materials according to the composition elements and mass percentages of perforated plugs described in Example 3 in Table 1, smelt, refine, pour, and process the raw materials; machine the processed plugs, and use phosphating solution to form phosphorus on the plug surface For the chemical film, the mass percentage of the phosphating solution is as follows: 22% phosphoric acid, 6% zinc oxide, 9% manganese nitrate, 10% dodecanol, and the balance is water. Then heat the plug to 910°C for annealing, keep it warm for 2 hours, then take it out of the furnace to cool at 320°C, and perform ZrN coating treatment on the coating machine to obtain the finished perforated plug. The target voltage of the coating machine is 450V, and the target power is 25W / CM 2 , the pulse bias voltage is 180V, the duty cycle is 80%, and the coating time is 25min.
PUM
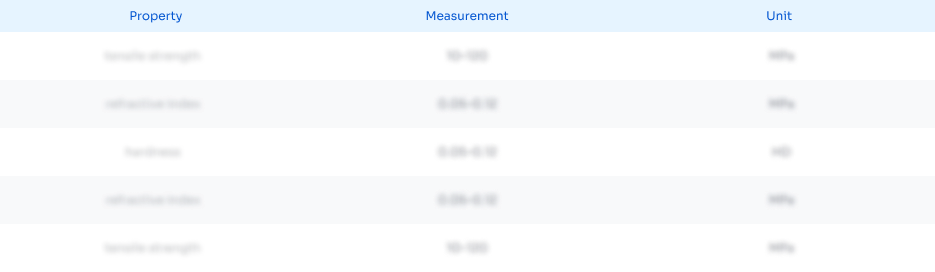
Abstract
Description
Claims
Application Information

- Generate Ideas
- Intellectual Property
- Life Sciences
- Materials
- Tech Scout
- Unparalleled Data Quality
- Higher Quality Content
- 60% Fewer Hallucinations
Browse by: Latest US Patents, China's latest patents, Technical Efficacy Thesaurus, Application Domain, Technology Topic, Popular Technical Reports.
© 2025 PatSnap. All rights reserved.Legal|Privacy policy|Modern Slavery Act Transparency Statement|Sitemap|About US| Contact US: help@patsnap.com