Embedded folding wing mechanism
A folding wing and embedded technology, which is applied in the fuselage, aircraft parts, aircraft control, etc., can solve the problems of limited application range, low strength, rigidity, shock resistance and precision requirements of folding wings, and inability to adapt to aircraft rudder folding, etc. To achieve the effect of simple and compact structure, reduced volume and reliable locking
- Summary
- Abstract
- Description
- Claims
- Application Information
AI Technical Summary
Problems solved by technology
Method used
Image
Examples
Embodiment Construction
[0023] The present invention will be further described below in conjunction with the accompanying drawings and embodiments, and the present invention includes but not limited to the following embodiments.
[0024] The embedded folding mechanism of the present invention is mainly composed of a seat body, a torsion spring, screw pins, gaskets, leaf springs, cylindrical pins, pin nuts, fins or rudder blades. This mechanism folds manually and unfolds automatically. In the folded state, the diameter is 3mm larger than the diameter of the cabin body. Put the folded part larger than the projectile diameter by 3mm into the corresponding guide groove of the launch tube, which is used for the axial positioning of the aircraft launch, and ensures that the wings (rudders) are folded in place. Utilize the torsion force of the torsion spring to make the wing (rudder) unfold instantly to ensure the aerodynamic characteristics of the rudder.
[0025] The embedded folding mechanism structure ...
PUM
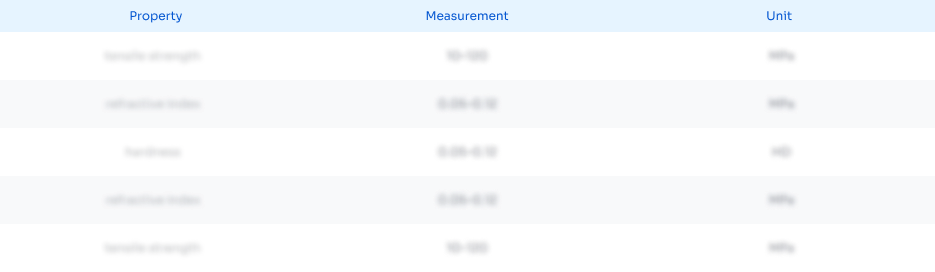
Abstract
Description
Claims
Application Information

- R&D
- Intellectual Property
- Life Sciences
- Materials
- Tech Scout
- Unparalleled Data Quality
- Higher Quality Content
- 60% Fewer Hallucinations
Browse by: Latest US Patents, China's latest patents, Technical Efficacy Thesaurus, Application Domain, Technology Topic, Popular Technical Reports.
© 2025 PatSnap. All rights reserved.Legal|Privacy policy|Modern Slavery Act Transparency Statement|Sitemap|About US| Contact US: help@patsnap.com