Universal rapid positioning detection tool for radiographic inspection of welded structural part
A technology of ray detection and welding structure, which is applied in the field of general rapid positioning and detection tooling, can solve the problems of inconvenient ray detection incidence angle and angle positioning, and achieve the effects of rapid adjustment of ray incidence angle, rapid installation and positioning, and improvement of radiation detection efficiency
- Summary
- Abstract
- Description
- Claims
- Application Information
AI Technical Summary
Problems solved by technology
Method used
Image
Examples
Embodiment 1
[0020] Embodiment 1, to figure 1 Radiographic inspection of No. 3 weld seam.
[0021] Found in the inspection tooling figure 2 As shown in the supporting surface of the assembled top block 4, press Figure 3a Place the weldment on the support surface of the tooling device as shown, and place the part in place;
[0022] Adjust the horizontal position of the circular tube where the weld seam is located on the base 2 according to the requirements of the radiographic inspection, and adjust the incident angle of rays required for the weld seam inspection;
[0023] After the parts are positioned, the No. 1 weld seam is transilluminated and arranged, and then the weld seam is subjected to radiographic inspection.
Embodiment 2
[0024] Embodiment 2, to figure 1 Radiographic Inspection of No.5 Weld Seam
[0025] Found in the inspection tooling figure 2 on groove 5 shown, press Figure 3b Place the weldment at the opening at the lowermost end of the groove as shown, and place the part in place;
[0026] According to the requirements of the incident angle of the ray detection, adjust the horizontal position of the circular tube where the weld seam is located in the groove 5, and adjust the incident angle of the weld seam;
[0027] After the parts are positioned, the No. 5 weld seam is arranged for transillumination, and the weld seam is subjected to radiographic inspection.
Embodiment 3
[0028] Embodiment 3, to figure 1 Radiographic Inspection of No. 2 Weld Seam
[0029] Found in the inspection tooling figure 2 As shown in the supporting surface 6 of the assembled top block 3, press Figure 3c Place the weldment on the support surface of the tooling device as shown, and place the part in place;
[0030] Adjust the horizontal position of the circular tube where the weld seam is located on the base 2 according to the requirements of the radiographic inspection, and adjust the incident angle of rays required for the weld seam inspection;
[0031] After the parts are positioned, the No. 2 weld seam is arranged for transillumination, and then the weld seam is subjected to radiographic inspection.
[0032] The positioning detection of the tooling of the present invention includes: step 1, according to the weld seam that needs to be detected in the welding structure, place the part on the support surface, fix it on the top block or place it in the groove for posi...
PUM
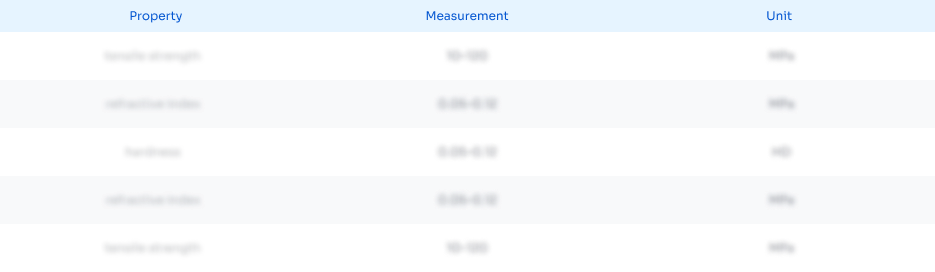
Abstract
Description
Claims
Application Information

- Generate Ideas
- Intellectual Property
- Life Sciences
- Materials
- Tech Scout
- Unparalleled Data Quality
- Higher Quality Content
- 60% Fewer Hallucinations
Browse by: Latest US Patents, China's latest patents, Technical Efficacy Thesaurus, Application Domain, Technology Topic, Popular Technical Reports.
© 2025 PatSnap. All rights reserved.Legal|Privacy policy|Modern Slavery Act Transparency Statement|Sitemap|About US| Contact US: help@patsnap.com