A kind of polyurethane resin for medium-soft organosilicon modified high-physical property surface layer and preparation method thereof
The technology of polyurethane resin and silicone is applied in the field of polyurethane resin and its preparation for modified high-physical property surface layer of medium-soft silicone, which can solve the problem of wear resistance, bending resistance, weak hydrolysis resistance, and hydroxyl silicone oil grafting rate of the polyurethane resin. It can ensure the flexural resistance, eliminate the existence of free small molecular silicone oil, and achieve the effect of soft hand feeling.
- Summary
- Abstract
- Description
- Claims
- Application Information
AI Technical Summary
Problems solved by technology
Method used
Image
Examples
Embodiment 1
[0057] Add 72 parts of polycarbonate polyol (molecular weight 2000) and 28 parts of polyether polyol (molecular weight 2000) into the reaction kettle, heat the reaction kettle to 100°C, dehydrate in vacuum for about 1 hour, and cool down to 50°C; Add 150 parts of dimethylformamide, 1.1 parts of 1,4-butanediol, 6.8 parts of ethylene glycol, and 35 parts of diphenylmethane diisocyanate, stir evenly, heat up to 70°C, and react for about 50 minutes; then add 6 Then, 4 parts of diphenylmethane diisocyanate were added at 70°C, reacted for 20 minutes, 0.02 part of organic bismuth catalyst was added, and the reaction was continued for 30 minutes; to the above In the reactor, the remaining 4.3 parts of diphenylmethane diisocyanate were added in batches to carry out chain extension reaction. The feeding interval of each step was 40-60 minutes, and the reaction temperature was 70 ° C. As the viscosity of the system increased, the remaining 478 parts of solvent were used to divide Three s...
Embodiment 2
[0064] Add 72 parts of polycarbonate polyol (molecular weight 2000) and 28 parts of polyether polyol (molecular weight 2000) into the reaction kettle, heat the reaction kettle to 100°C, dehydrate in vacuum for about 1 hour, and cool to 50°C; Add 150 parts of dimethylformamide, 1.1 parts of 1,4-butanediol, 6.8 parts of ethylene glycol, and 35 parts of diphenylmethane diisocyanate, stir evenly, raise the temperature to 70°C, and react for about 50 minutes; then add 3 Then, 4 parts of diphenylmethane diisocyanate were added at 70°C, reacted for 20 minutes, 0.02 part of organic bismuth catalyst was added, and the reaction was continued for 30 minutes; to the above In the reactor, the remaining 4.2 parts of diphenylmethane diisocyanate were added in batches to carry out chain extension reaction, the feeding interval of each step was 40-60 minutes, and the reaction temperature was 70 ° C. As the viscosity of the system increased, the remaining 466 parts of solvent were used to divide...
PUM
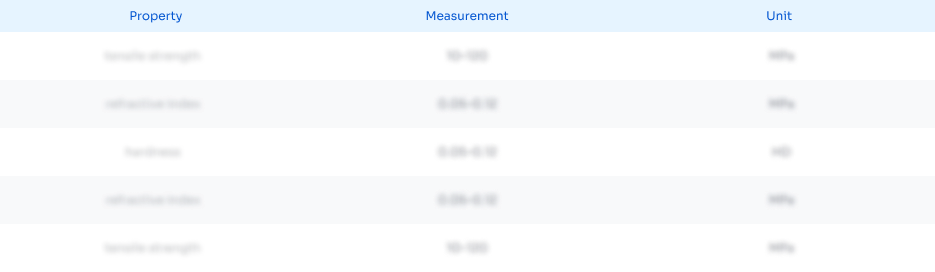
Abstract
Description
Claims
Application Information

- R&D
- Intellectual Property
- Life Sciences
- Materials
- Tech Scout
- Unparalleled Data Quality
- Higher Quality Content
- 60% Fewer Hallucinations
Browse by: Latest US Patents, China's latest patents, Technical Efficacy Thesaurus, Application Domain, Technology Topic, Popular Technical Reports.
© 2025 PatSnap. All rights reserved.Legal|Privacy policy|Modern Slavery Act Transparency Statement|Sitemap|About US| Contact US: help@patsnap.com