Washing system and method for tail gas of blower cooling tank area
A tail gas scrubbing system and tail gas technology are applied in separation methods, chemical instruments and methods, and dispersed particle separation, etc., which can solve problems such as difficult recovery of tail gas in tank areas, negative pressure gas pipelines, increased difficulty of tail gas recovery, and lack of tail gas recovery systems. Achieve the effect of meeting the requirements of environmental protection situation and reducing the occupational hazard risk of employees
- Summary
- Abstract
- Description
- Claims
- Application Information
AI Technical Summary
Problems solved by technology
Method used
Image
Examples
Embodiment Construction
[0028] The specific embodiment of the present invention will be further described below in conjunction with accompanying drawing:
[0029] Such as figure 1 As shown, a tail gas washing system in the drum cold tank area includes a water washing tower 1, an acid washing tower 2, an alkali washing tower 3, an activated carbon adsorption tower 4, a fan 5 and an tail gas pipeline.
[0030] The water washing tower 1, the acid washing tower 2, the alkali washing tower 3 and the activated carbon adsorption tower 4 are connected in series through pipelines in sequence, and after being connected in series, they are connected to the tail gas pipeline through the first connecting pipe 6, and the fan is installed on the first connecting pipe 6. The water washing tower 1, the pickling tower 2, and the alkali washing tower 3 all contain two spraying liquid pumps 7 and auxiliary spraying and external discharge process pipes and valves.
[0031] The water washing tower 1 uses the water in the...
PUM
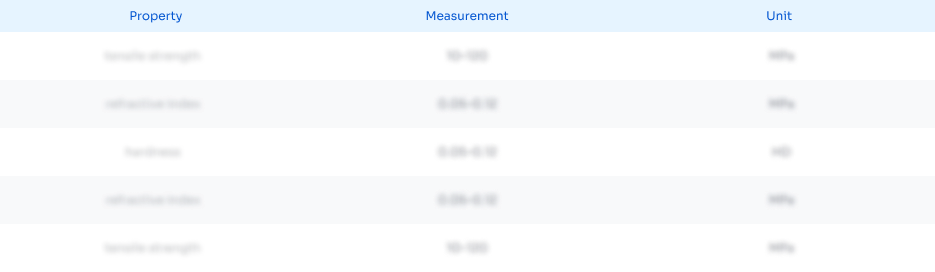
Abstract
Description
Claims
Application Information

- Generate Ideas
- Intellectual Property
- Life Sciences
- Materials
- Tech Scout
- Unparalleled Data Quality
- Higher Quality Content
- 60% Fewer Hallucinations
Browse by: Latest US Patents, China's latest patents, Technical Efficacy Thesaurus, Application Domain, Technology Topic, Popular Technical Reports.
© 2025 PatSnap. All rights reserved.Legal|Privacy policy|Modern Slavery Act Transparency Statement|Sitemap|About US| Contact US: help@patsnap.com