Excavator construction guiding system and construction method
A technology of guidance system and construction method, applied in the field of surveying, can solve the problems of occlusion of viewing angle, inconvenience, and many uncertain factors of environmental change, and achieve the effect of avoiding over-excavation and convenient maintenance.
- Summary
- Abstract
- Description
- Claims
- Application Information
AI Technical Summary
Problems solved by technology
Method used
Image
Examples
Embodiment
[0035] Such as figure 1 As shown, an excavator construction guidance system includes an excavator body 1, a boom 2, a stick 3, and a bucket 4. The excavator is equipped with a positioning module and a measuring stick for measuring and estimating the pose information of the boom 2 The measuring assembly for the telescopic length of the hydraulic cylinder 14 and / or the bucket hydraulic cylinder 15 also includes a measuring terminal.
[0036] The measurement terminal can be specifically a computer, which can receive the measurement information of the positioning module and measurement components through the serial port; calculate the position and orientation information of the boom 2, stick 3 and bucket 4 according to the measurement information; use software to establish the terrain model of the construction site and the bucket 4 simulation model, and determine the pose of the bucket 4 simulation model according to the pose information of the bucket 4, thereby determining the po...
PUM
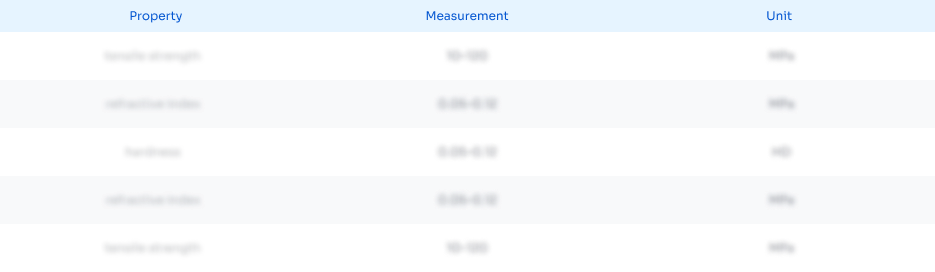
Abstract
Description
Claims
Application Information

- R&D
- Intellectual Property
- Life Sciences
- Materials
- Tech Scout
- Unparalleled Data Quality
- Higher Quality Content
- 60% Fewer Hallucinations
Browse by: Latest US Patents, China's latest patents, Technical Efficacy Thesaurus, Application Domain, Technology Topic, Popular Technical Reports.
© 2025 PatSnap. All rights reserved.Legal|Privacy policy|Modern Slavery Act Transparency Statement|Sitemap|About US| Contact US: help@patsnap.com