Fluid flow velocity sensor and system based on surface acoustic waves
A technology of fluid flow velocity and surface acoustic wave, applied in the field of fluid sensing, can solve the problems of large buoy volume, measurement error and low sensitivity of the fluid to be measured
- Summary
- Abstract
- Description
- Claims
- Application Information
AI Technical Summary
Problems solved by technology
Method used
Image
Examples
Embodiment 1
[0031] The present invention provides a fluid velocity sensor based on surface acoustic waves. The fluid velocity sensor comprises: a base 1, a first electrode 21, and a second electrode 22; There is a fluid channel 3, a section of the inner wall of the fluid channel 3 is provided with an adhesive layer 4, and the first electrode 21 and the second electrode 22 are respectively arranged on both sides of the fluid channel 3; the material of the first electrode 21 and the second electrode 22 is conductive Metal material, the material of the adhesive layer 4 is a fluid adhesive material, and the material of the substrate 1 is a piezoelectric material.
[0032]The shape of the base 1 can be a cube, it can be a cuboid, and it can also be a truss. There is a fluid channel 3. The cross-sectional area and shape of the fluid channel 3 are set according to actual needs, and are not specifically limited here. The two sides of the fluid channel 3 are respectively provided with a first elec...
Embodiment 2
[0047] Based on Embodiment 1, this embodiment of the present application provides another surface acoustic wave-based fluid velocity sensor. It is basically the same as Embodiment 1, the only difference is that the thickness of the fluid channel 3 of the fluid velocity sensor is decreasing.
[0048] After the fluid to be tested passes through the fluid channel 3 , it will be adhered to the adhesive layer 4 . The amount of adhesion is related to the fluid flow rate. When the first electrode 21 applies an excitation signal, a surface acoustic wave will be generated on the surface of the substrate 1, and the surface acoustic wave passes through the fluid channel 3 during propagation, and is affected by the adhesive fluid of the adhesive layer 4, so that the dielectric constant of the substrate 1 A corresponding change occurs, resulting in a corresponding change in the frequency of the surface acoustic wave. Since the flow velocity of the fluid corresponds to the frequency of th...
Embodiment 3
[0050] figure 2 Another surface acoustic wave-based fluid flow velocity sensor provided by an embodiment of the present invention is based on embodiment 2, and this application embodiment provides another surface acoustic wave-based fluid flow velocity sensor. It is basically the same as Embodiment 2, except that there are multiple adhesive layers 4 in the fluid channel 3 of the fluid flow sensor. For clarity, the number of the adhesive layers 4 is two for illustration.
[0051] Optionally, there may be multiple adhesive layers 4 in the fluid channel 3 of the fluid velocity sensor. This makes it easier to stick fluids.
[0052] After the fluid to be tested passes through the fluid channel 3 , it will be adhered to the adhesive layer 4 . The amount of adhesion is related to the fluid flow rate. When the first electrode 21 and the second electrode 22 apply an excitation signal, a surface acoustic wave will be generated on the surface of the substrate 1, and the surface acous...
PUM
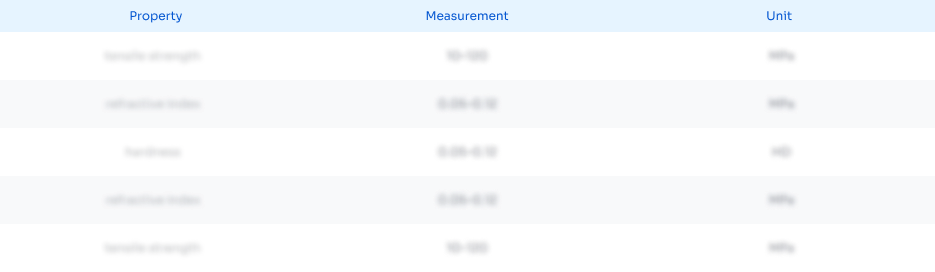
Abstract
Description
Claims
Application Information

- Generate Ideas
- Intellectual Property
- Life Sciences
- Materials
- Tech Scout
- Unparalleled Data Quality
- Higher Quality Content
- 60% Fewer Hallucinations
Browse by: Latest US Patents, China's latest patents, Technical Efficacy Thesaurus, Application Domain, Technology Topic, Popular Technical Reports.
© 2025 PatSnap. All rights reserved.Legal|Privacy policy|Modern Slavery Act Transparency Statement|Sitemap|About US| Contact US: help@patsnap.com