Manufacturing equipment main shaft bearing health assessment method based on probability description and spectral analysis
A spindle bearing and health assessment technology, applied in probabilistic CAD, special data processing applications, instruments, etc., can solve problems such as insensitivity, data over-reliance on early failures, etc., and achieve the effect of overcoming over-dependence
- Summary
- Abstract
- Description
- Claims
- Application Information
AI Technical Summary
Problems solved by technology
Method used
Image
Examples
Embodiment 1
[0078] The whole life cycle data set in Example 1 contains a total of 984 files, the experimental sampling frequency is 20kHz, the shaft rotation frequency is 33.33Hz, and the data is collected every 10 minutes. At the end of the experiment, it is found that the outer ring of the main shaft bearing has a serious failure. The bearing outer ring theory The characteristic frequency is about 236Hz.
[0079] Such as figure 1 Shown is a step-by-step flowchart of a method for evaluating the health of spindle bearings in manufacturing equipment based on probability description and spectral analysis, including the following steps:
[0080] (1) Feature extraction
[0081] According to the sampling frequency and the spindle speed, the sampling points for each rotation of the spindle are about 600 points, and the data of each file is intercepted by 1200 points and 16 segmented signals;
[0082] After 4-layer WPT decomposition of the segmented signal, the last layer of node signal is rec...
Embodiment 2
[0109] The full life cycle data set of Example 2 contains 161 files in total, the experimental sampling frequency is 25.6kHz, the shaft rotation frequency is 35Hz, and the data is collected every 1 minute. At the end of the experiment, it is found that the outer ring of the main shaft bearing has a serious failure. The outer ring of the main shaft bearing The theoretical characteristic frequency is about 108Hz.
[0110] (1) Feature extraction
[0111] According to the sampling frequency and the spindle speed, the sampling points for each rotation of the spindle are about 731 points, and the data of each file is divided into 1462 points to intercept 16 segmented signals;
[0112] After 4-layer WPT decomposition of the segmented signal, the last layer of node signal is reconstructed to obtain 16-segment signal components;
[0113] Demodulate each segmented signal and the reconstructed signal of the last WPT node to obtain 17 envelope signals, and calculate the ESGI index of the...
PUM
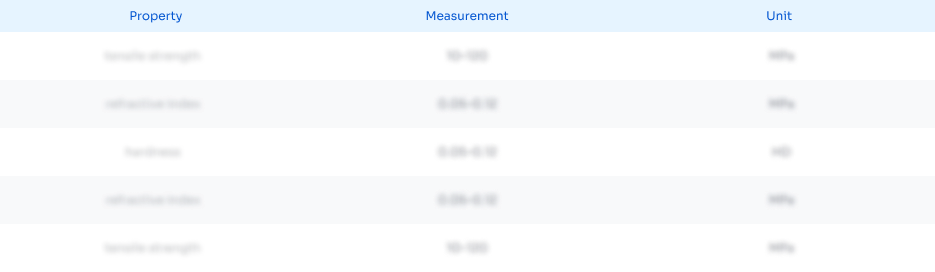
Abstract
Description
Claims
Application Information

- R&D
- Intellectual Property
- Life Sciences
- Materials
- Tech Scout
- Unparalleled Data Quality
- Higher Quality Content
- 60% Fewer Hallucinations
Browse by: Latest US Patents, China's latest patents, Technical Efficacy Thesaurus, Application Domain, Technology Topic, Popular Technical Reports.
© 2025 PatSnap. All rights reserved.Legal|Privacy policy|Modern Slavery Act Transparency Statement|Sitemap|About US| Contact US: help@patsnap.com