Method for preparing battery-grade lithium carbonate and iron phosphate by recycling lithium iron phosphate cathode waste
A technology for lithium iron phosphate and waste recycling, applied in lithium carbonate;/acid carbonate, waste collector recycling, chemical instruments and methods, etc., can solve the problems of lithium recovery rate decline and large consumption, To achieve the effect of good product quality
- Summary
- Abstract
- Description
- Claims
- Application Information
AI Technical Summary
Problems solved by technology
Method used
Examples
Embodiment 1
[0017] Add the lithium iron phosphate positive electrode waste powder into water to make a slurry, blow in air and stir, and control the oxidation leaching conditions with a solid-liquid ratio of 500g / L, a reaction time of 1 hour, and a reaction temperature of 25°C. Slowly add oxalic acid during the process to maintain The pH is 5.0. After the reaction is completed, filter and separate, adjust the pH of the filtrate to 11 to precipitate and remove impurities, then heat the solution to 95°C, and add saturated sodium carbonate solution to precipitate lithium carbonate at the same time, and the filtered solid product is washed and dried to obtain lithium carbonate product. Add iron powder and a small amount of phosphoric acid to the water leaching slag and put it into a planetary ball mill for ball milling activation. The molar amount of iron powder added is 0.55 times the molar amount of iron in the water leaching slag, and the ball milling time is 1 hour; the product after ball ...
Embodiment 2
[0019] Add the lithium iron phosphate positive electrode waste powder into water to make a slurry, blow in air and stir, control the oxidation leaching condition with a solid-liquid ratio of 350g / L, a reaction time of 3 hours, and a reaction temperature of 50°C. Slowly add acetic acid during the process to maintain The pH is around 3.5. After the reaction is completed, solid-liquid separation is carried out to obtain lithium-containing solution and leaching residue, and the leaching rate of lithium is 98.9%. Adjust the pH of the filtrate to 11 to precipitate and remove impurities, then heat the solution to 95°C, and add saturated sodium carbonate solution to precipitate lithium carbonate at the same time, and the filtered solid product is washed and dried to obtain lithium carbonate product. Add iron powder to the water leaching slag and add a small amount of phosphoric acid into a planetary ball mill for ball milling activation. The molar amount of iron powder added is 0.575 ...
Embodiment 3
[0021] Add the lithium iron phosphate positive electrode waste powder into water to make a slurry, blow in air and stir, control the oxidation leaching condition with a solid-to-liquid ratio of 200g / L, a reaction time of 5 hours, and a reaction temperature of 90°C. Slowly add citric acid during the process Maintain pH around 4.0. After the reaction is completed, solid-liquid separation is carried out to obtain lithium-containing solution and leaching residue, and the leaching rate of lithium is 99.2%. Adjust the pH of the filtrate to 11 to precipitate and remove impurities, then heat the solution to 95°C, and add saturated sodium carbonate solution to precipitate lithium carbonate at the same time, and the filtered solid product is washed and dried to obtain lithium carbonate product. Add iron powder and a small amount of phosphoric acid to the water leaching slag and put it into a planetary ball mill for ball milling activation. The molar amount of iron powder added is 0.6 ti...
PUM
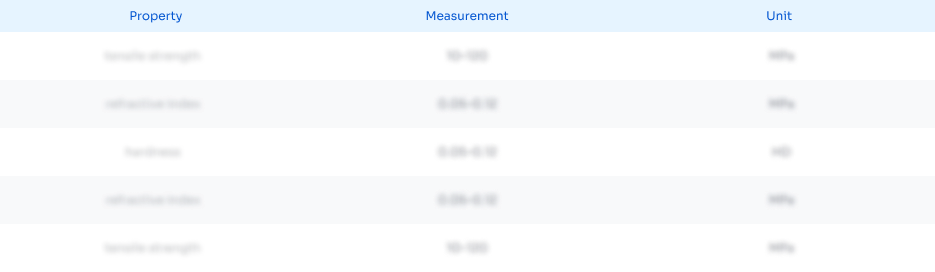
Abstract
Description
Claims
Application Information

- R&D
- Intellectual Property
- Life Sciences
- Materials
- Tech Scout
- Unparalleled Data Quality
- Higher Quality Content
- 60% Fewer Hallucinations
Browse by: Latest US Patents, China's latest patents, Technical Efficacy Thesaurus, Application Domain, Technology Topic, Popular Technical Reports.
© 2025 PatSnap. All rights reserved.Legal|Privacy policy|Modern Slavery Act Transparency Statement|Sitemap|About US| Contact US: help@patsnap.com