Machining process and die for injection piston body
A technology of injection piston and processing technology, applied in the field of mechanical forging, can solve the problems of high production cost and poor stability, achieve the effect of high precision and avoid assembly errors
- Summary
- Abstract
- Description
- Claims
- Application Information
AI Technical Summary
Problems solved by technology
Method used
Image
Examples
Embodiment
[0028] A kind of mold of injection piston body, see attached figure 1 , including an upper mold body 1 and a lower mold body 2, the upper mold body 1 has a basic cavity 11 for forming a basic piston body, and the lower mold body 2 is provided with a variable cavity 21 for extending the length of the piston rod, wherein the change is set in the variable type The thickness of the insert 3 in the cavity 21 can realize changing the length of the piston rod to be forged. The upper mold body 1 and the lower mold body 2 are fixed by bolts 4 .
[0029] When forging, the extrusion force of the basic cavity 11 is relatively large, so that the deformation of the basic cavity 11 is relatively large, but since the basic cavity 11 and the variable cavity 21 are arranged separately, and the variable cavity 21 is located below, When forging, the extrusion force that the variable cavity 21 bears is very small, and the variable cavity 21 hardly produces expansion deformation, and then there is...
PUM
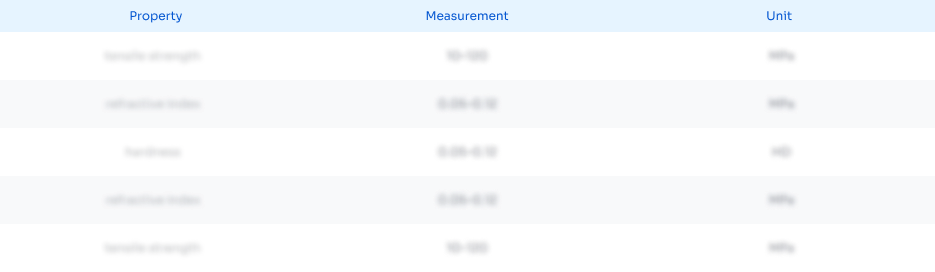
Abstract
Description
Claims
Application Information

- Generate Ideas
- Intellectual Property
- Life Sciences
- Materials
- Tech Scout
- Unparalleled Data Quality
- Higher Quality Content
- 60% Fewer Hallucinations
Browse by: Latest US Patents, China's latest patents, Technical Efficacy Thesaurus, Application Domain, Technology Topic, Popular Technical Reports.
© 2025 PatSnap. All rights reserved.Legal|Privacy policy|Modern Slavery Act Transparency Statement|Sitemap|About US| Contact US: help@patsnap.com