Skylight guide rail finish sawing machine gauge
A technology of precision sawing machine and guide rail, which is applied to the inspection tool field of skylight guide rail precision sawing machine, can solve the problems of non-uniform product cross-section, unguaranteed precision, non-uniform sawing length, etc., to improve detection efficiency, facilitate worker management, and facilitate The effect of data logging
- Summary
- Abstract
- Description
- Claims
- Application Information
AI Technical Summary
Problems solved by technology
Method used
Image
Examples
Embodiment Construction
[0022] Below in conjunction with specific embodiment, further illustrate the present invention. It should be understood that these examples are only used to illustrate the present invention and are not intended to limit the scope of the present invention. In addition, it should be understood that after reading the teachings of the present invention, those skilled in the art may make various changes or modifications to the present invention, and these equivalent forms also fall within the scope defined by the appended claims of the present application.
[0023] The embodiment of the present invention relates to a skylight guide rail fine saw machine inspection tool, such as figure 1 As shown in -2, when the technical solution was working, at first the preparatory work was carried out before the detection, and the positioning end sliding detection block 11 on the positioning end detection assembly 8, the translation end sliding detection block 20 on the translation end detection...
PUM
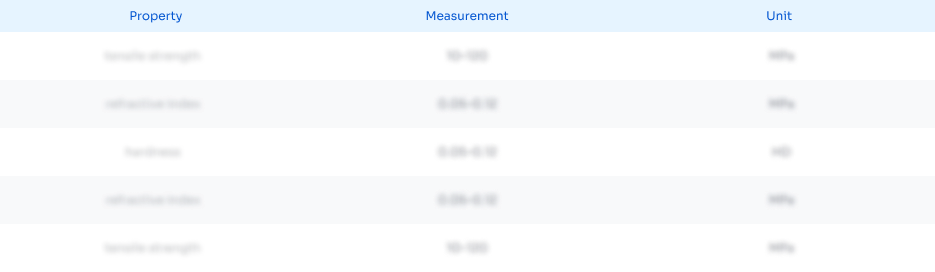
Abstract
Description
Claims
Application Information

- Generate Ideas
- Intellectual Property
- Life Sciences
- Materials
- Tech Scout
- Unparalleled Data Quality
- Higher Quality Content
- 60% Fewer Hallucinations
Browse by: Latest US Patents, China's latest patents, Technical Efficacy Thesaurus, Application Domain, Technology Topic, Popular Technical Reports.
© 2025 PatSnap. All rights reserved.Legal|Privacy policy|Modern Slavery Act Transparency Statement|Sitemap|About US| Contact US: help@patsnap.com