A cantilever beam-type active-passive integrated orthogonal six-degree-of-freedom vibration isolation device
A degree of freedom, active and passive technology, used in motor vehicles, transportation and packaging, non-rotational vibration suppression, etc., can solve the problems of difficult to achieve decoupling, large size, heavy weight, etc. Stiffness decoupling to achieve lightweight effect
- Summary
- Abstract
- Description
- Claims
- Application Information
AI Technical Summary
Problems solved by technology
Method used
Image
Examples
Embodiment Construction
[0057] The present invention will be described in further detail below in conjunction with the accompanying drawings and specific embodiments.
[0062]
[0065] J
[0066] J is the Jacobian matrix of the Stewart platform.
[0076] The carbon fiber rod (3), the preferred scheme is specifically: a hollow carbon fiber having an outer diameter of preferably 40mm and a thickness of 1.5mm
[0078] The two positioning balls are provided with through holes along the diameter direction of the balls, corresponding to the positions of the arc through holes between the two ball sockets;
[0080] The ball center distance of the two ball sockets is preferably required to be a situation that does not affect the swing interference of the two movable ends within the range of ±0.2°
[0083] The positioning ball is provided with a through hole along the diameter of the ball, corresponding to the position of the arc-shaped through hole between the two ball sockets; positioning
[0091] The four sides ...
PUM
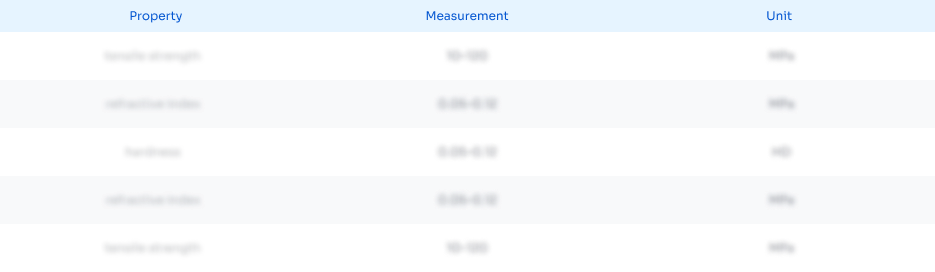
Abstract
Description
Claims
Application Information

- R&D
- Intellectual Property
- Life Sciences
- Materials
- Tech Scout
- Unparalleled Data Quality
- Higher Quality Content
- 60% Fewer Hallucinations
Browse by: Latest US Patents, China's latest patents, Technical Efficacy Thesaurus, Application Domain, Technology Topic, Popular Technical Reports.
© 2025 PatSnap. All rights reserved.Legal|Privacy policy|Modern Slavery Act Transparency Statement|Sitemap|About US| Contact US: help@patsnap.com