On-machine inspection system and method for automatic tool focus adjustment based on machine vision
A detection system and machine vision technology, applied in the direction of manufacturing tools, measuring/indicating equipment, metal processing machinery parts, etc., can solve the problems of low detection efficiency, troublesome detection process, large space occupation, etc., to ensure rotation accuracy and stability , versatility and applicability improvement, and the effect of saving internal space
- Summary
- Abstract
- Description
- Claims
- Application Information
AI Technical Summary
Problems solved by technology
Method used
Image
Examples
Embodiment 1
[0109] This embodiment provides an automatic tool based on machine vision focus detection system in the machine, with reference to attached figure 2 with figure 2 (A), the six detection system consists of extension drive device I, II webs, hexagon socket head cap screws III, IV hexagon socket head screws, hexagon socket head cap screws V and VI image pickup device composed of . Wherein the connecting plate is connected to one end of the I II by hexagon socket head cap screws III and IV hexagon socket head screws with the driving means. After installing the drive coupling plate II overall vertical distribution means I, I drive means can drive the rotation of the link plate II, II may be driven up and down movement of the connecting plate. Image pickup device VI is attached to the other end of the link plate II, which is set into the mounting hole from above the web II, II to Jiazhu web and to achieve both connection and positioning between the cylinder head by screws V.
[0110] Re...
Embodiment 2
[0126] This embodiment provides a method based on machine vision tools automatic focusing system of the working machine testing method, the current machining center tool most of the drill mill, with the cutter, for example, in the form of a special milling tool wear, In addition to flank wear, the cutter after Vice flank wear is also more serious, therefore the formulation of blunt criteria should take into account the tool flank wear deputy. Therefore, to deal with the image sensing edge and the end face of the drill mill is acquired during the image acquisition, and also to respond to the machine tool diameter is measured. One purpose of the installation to ensure that machine tool bed model is correct, to avoid staff negligence installed the wrong tool, the second is in accordance with the measured current actual diameter of the tool as a basis for the user to dynamically modify the parameters of the NC program. However, due to the machining center tool wide range of different ...
PUM
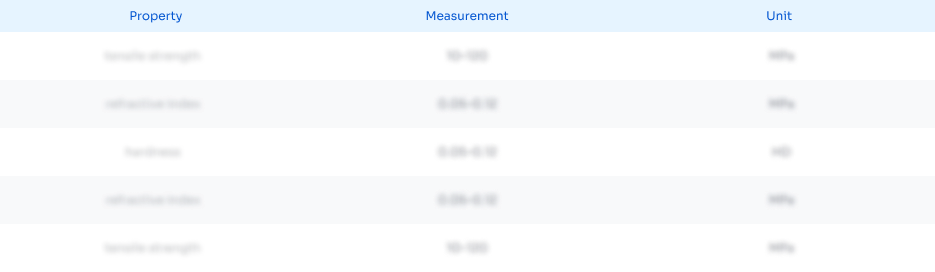
Abstract
Description
Claims
Application Information

- R&D Engineer
- R&D Manager
- IP Professional
- Industry Leading Data Capabilities
- Powerful AI technology
- Patent DNA Extraction
Browse by: Latest US Patents, China's latest patents, Technical Efficacy Thesaurus, Application Domain, Technology Topic, Popular Technical Reports.
© 2024 PatSnap. All rights reserved.Legal|Privacy policy|Modern Slavery Act Transparency Statement|Sitemap|About US| Contact US: help@patsnap.com