Integral annular casing numerical control machining optimization method based on surface roughness control
A surface roughness and optimization method technology, applied in the direction of digital control, program control, electrical program control, etc., can solve the problems of low processing efficiency, difficult to guarantee processing accuracy, and difficult to control stability, so as to achieve high processing quality and improve processing quality. The effect of shortening the quality and processing time
- Summary
- Abstract
- Description
- Claims
- Application Information
AI Technical Summary
Problems solved by technology
Method used
Image
Examples
Embodiment Construction
[0039] The invention will be further described below in conjunction with the accompanying drawings and specific implementation examples.
[0040] Such as figure 1 As shown, a method for optimizing the numerical control machining of an integral ring casing based on surface roughness control includes the following steps:
[0041] Step 1: According to the integral ring casing parts to be processed, use UG to write the initial CNC machining program, and construct the simulation model of the integral ring casing parts to be processed;
[0042] Step 2: Import the simulation model of the integral ring casing part to be processed and the initial NC machining program written into the geometric simulation software Vericut, input the information of the machine tool control system, simulate the real machining process, and perform geometric analysis on the written initial NC machining program. Simulation analysis, according to the simulation processing model generated by simulation, check...
PUM
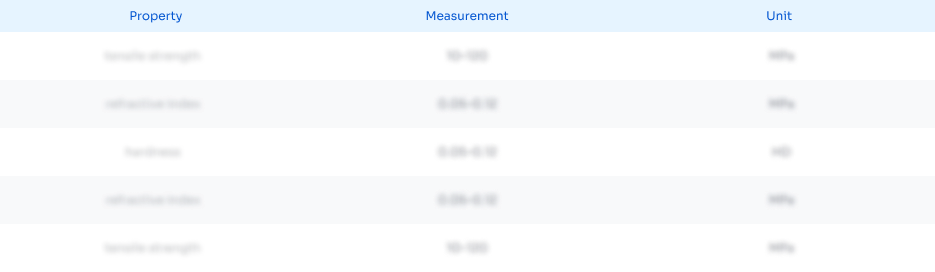
Abstract
Description
Claims
Application Information

- R&D
- Intellectual Property
- Life Sciences
- Materials
- Tech Scout
- Unparalleled Data Quality
- Higher Quality Content
- 60% Fewer Hallucinations
Browse by: Latest US Patents, China's latest patents, Technical Efficacy Thesaurus, Application Domain, Technology Topic, Popular Technical Reports.
© 2025 PatSnap. All rights reserved.Legal|Privacy policy|Modern Slavery Act Transparency Statement|Sitemap|About US| Contact US: help@patsnap.com