Mixed sulfur circulating hydrogen production method
A technology of sulfur cycle and dilute sulfuric acid, applied in electrolysis process, electrolysis components, etc., can solve the problems of high water consumption in hydrogen production from fossil fuels, underutilization of by-product gas, unsatisfactory high energy density heat source of sulfuric acid, etc., to achieve Improve economic efficiency and alleviate the effect of high water consumption
- Summary
- Abstract
- Description
- Claims
- Application Information
AI Technical Summary
Problems solved by technology
Method used
Image
Examples
Embodiment 1
[0033] Adopting the solution of the present invention, nuclear energy is used as primary energy, and a mixed sulfur cycle hydrogen production process suitable for the iron and steel industry is designed: the dilute sulfuric acid from the depolarized electrolytic cell is divided into two streams, and one of the dilute sulfuric acid is sent to rectification Tower, rectification and enrichment to 70%. The high-temperature steam generated by the high-temperature air-cooled nuclear reactor is used. After the concentrated sulfuric acid is preheated to 400°C in the heat exchanger, it is mixed with coke oven gas and air from the coking oven of the steel plant and enters the cracking furnace for high-temperature cracking. The cracking temperature is 1000°C. Pressure 0.1MPa, get SO 2 , CO 2 、H 2 O mixed gas. The above mixed gas is pressurized to 1.0Mpa in the pressurized cooling tower, and cooled to 80°C, part of the water is separated, and sent to the cathode of the depolarization e...
Embodiment 2
[0037] Adopting the solution of the present invention, nuclear energy is used as the primary energy source to design a mixed sulfur cycle hydrogen production process suitable for the hydrofining of oil products in the petrochemical industry: the dilute sulfuric acid from the depolarization electrolytic cell is divided into two streams, one of which is dilute The sulfuric acid is sent to the rectification tower, where it is concentrated to 90%. The high-temperature steam generated by the high-temperature air-cooled nuclear reactor is used. After the concentrated sulfuric acid is preheated to 550°C in the heat exchanger, it is mixed with the reformed dry gas and air from the refinery unit and enters the cracking furnace for high-temperature cracking. The cracking temperature is 1250°C and the pressure is high. 0.4MPa, get SO 2 , CO 2 、H 2 O mixed gas. The above mixed gas is pressurized to 1.0Mpa in the pressurized cooling tower, and cooled to 80°C, part of the water is separa...
Embodiment 3
[0041] Adopting the solution of the present invention, using solar heat collection and natural gas as primary energy, the process flow of mixed sulfur cycle hydrogen production is designed: the dilute sulfuric acid from the depolarized electrolytic cell is divided into two streams, and one of the dilute sulfuric acid is sent to the rectification tower , Distilled and concentrated to 80%. Using high-temperature steam generated by solar heat collectors, preheat concentrated sulfuric acid to 450°C in a heat exchanger, mix it with natural gas and air, and enter the cracking furnace for high-temperature cracking. The cracking temperature is 1100°C and the pressure is 0.2MPa to obtain SO 2 , CO 2 、H 2 O mixed gas. The above mixed gas is pressurized to 1.0Mpa in the pressurized cooling tower and cooled to 80°C, part of the water is separated and sent to the cathode of the depolarization electrolysis cell. The remaining unliquefied gas enters the absorption tower, is absorbed by an...
PUM
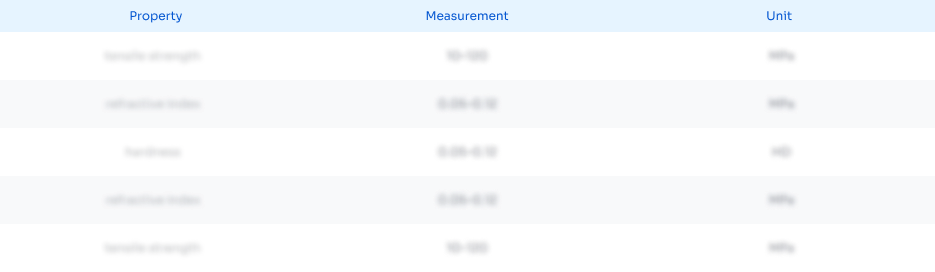
Abstract
Description
Claims
Application Information

- R&D
- Intellectual Property
- Life Sciences
- Materials
- Tech Scout
- Unparalleled Data Quality
- Higher Quality Content
- 60% Fewer Hallucinations
Browse by: Latest US Patents, China's latest patents, Technical Efficacy Thesaurus, Application Domain, Technology Topic, Popular Technical Reports.
© 2025 PatSnap. All rights reserved.Legal|Privacy policy|Modern Slavery Act Transparency Statement|Sitemap|About US| Contact US: help@patsnap.com