Method for preparing manganese sulfate and battery-grade manganese sulfate by using manganese-containing ore
A technology of manganese sulfate and manganese ore, which is applied in the field of metallurgy, can solve the problems of reducing equipment use efficiency, uncontrollable leaching reaction rate, consumption of sulfuric acid, etc., and achieves the effects of low cost, easy separation and purification, and high extraction rate
- Summary
- Abstract
- Description
- Claims
- Application Information
AI Technical Summary
Benefits of technology
Problems solved by technology
Method used
Examples
Embodiment 1
[0043] The invention provides a kind of method utilizing manganese-containing ore to prepare manganese sulfate, comprising the following steps:
[0044] Step 1: Pulverize the rhodochrosite ore, calcinate it at 600°C for 24 hours, then clinker it, then pulverize it with a pulverizer, pass it through a 100-mesh sieve, and collect the sieved material;
[0045] Step 2: Put the material with a mass of 1000g into the fixed bed reactor, and feed the mixed gas of sulfur dioxide, oxygen and water vapor with a volume ratio of 1:2:2. When the concentration of sulfur dioxide at the inlet of the reactor is not much different from the concentration at the outlet , that is, the difference between the concentration of sulfur dioxide at the inlet and the concentration of sulfur dioxide at the outlet is ±5%, stop feeding the mixed gas;
[0046] Step 3: The reacted material is washed with deionized water with a solid-to-liquid ratio of 1:5, coarsely filtered with a coarse filter, and finely filt...
Embodiment 2
[0050] The invention provides a kind of method utilizing manganese-containing ore to prepare manganese sulfate, comprising the following steps:
[0051] Step 1: Pulverize the rhodochrosite ore, calcinate it at 700°C for 12 hours, then clinker it, then pulverize it with a pulverizer, pass it through a 200-mesh sieve, and collect the sieved material;
[0052] Step 2: Put the material with a mass of 1000g into the fixed bed reactor, and feed the mixed gas of sulfur dioxide, oxygen and water vapor with a volume ratio of 1:2:2. When the concentration of sulfur dioxide at the inlet of the reactor is not much different from the concentration at the outlet , that is, the difference between the concentration of sulfur dioxide at the inlet and the concentration of sulfur dioxide at the outlet is ±5%, stop feeding the mixed gas;
[0053] Step 3: The reacted material is washed with deionized water with a solid-to-liquid ratio of 1:4, coarsely filtered with a coarse filter, and finely filt...
Embodiment 3
[0057] The invention provides a kind of method utilizing manganese-containing ore to prepare manganese sulfate, comprising the following steps:
[0058] Step 1: Pulverize the rhodochrosite ore, calcinate it at 800°C for 8 hours, then clinker it, then pulverize it with a pulverizer, pass it through a 300-mesh sieve, and collect the sieved material;
[0059] Step 2: Put the material with a mass of 1000g into the fixed bed reactor, and feed the mixed gas of sulfur dioxide, oxygen and water vapor with a volume ratio of 1:2:2. When the concentration of sulfur dioxide at the inlet of the reactor is not much different from the concentration at the outlet , that is, the difference between the concentration of sulfur dioxide at the inlet and the concentration of sulfur dioxide at the outlet is ±5%, stop feeding the mixed gas;
[0060] Step 3: The reacted material is washed with deionized water with a solid-to-liquid ratio of 1:3, coarsely filtered with a coarse filter, and finely filte...
PUM
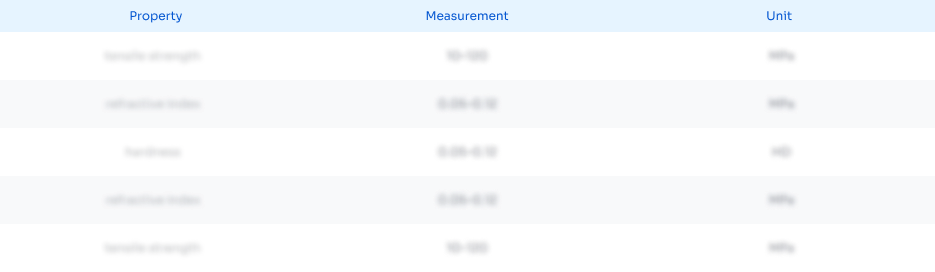
Abstract
Description
Claims
Application Information

- R&D
- Intellectual Property
- Life Sciences
- Materials
- Tech Scout
- Unparalleled Data Quality
- Higher Quality Content
- 60% Fewer Hallucinations
Browse by: Latest US Patents, China's latest patents, Technical Efficacy Thesaurus, Application Domain, Technology Topic, Popular Technical Reports.
© 2025 PatSnap. All rights reserved.Legal|Privacy policy|Modern Slavery Act Transparency Statement|Sitemap|About US| Contact US: help@patsnap.com