Sand core with built-in pouring gate
A built-in, sand core technology, applied in the direction of mold cores, casting molding equipment, metal processing equipment, etc., can solve problems such as meat loss, large stubble, and trachoma on the end face of castings
- Summary
- Abstract
- Description
- Claims
- Application Information
AI Technical Summary
Problems solved by technology
Method used
Image
Examples
Embodiment Construction
[0017] The present invention will be further described below in conjunction with the accompanying drawings and specific embodiments.
[0018] see figure 1 , the present invention takes the three-way malleable iron connector as an example, including a resin sand core 2 arranged in the sand mold 1, a gate 4 is arranged in the resin sand core, and one end of the gate 4 provided in the resin sand core 2 It is connected with the runner 3 in the sand mold 1, and the other end is connected with the cavity 5 of the malleable iron connector formed by the sand mold 1 and the resin sand core 2. The shape of the gate 4 is with a certain arc, close to the injection direction of the runner 3 The cross-sectional area A-A of the gate 4 is larger than the cross-sectional area B-B of the gate close to the cavity forming the malleable iron connector. The cross-sectional area A-A of the gate is higher than the cross-sectional area B-B of the gate. When pouring, the liquid metal flows in from the ...
PUM
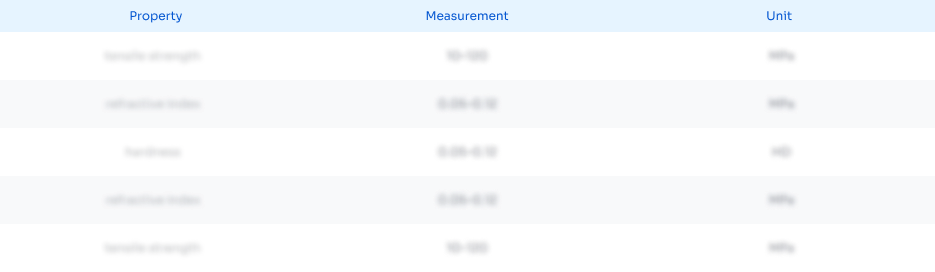
Abstract
Description
Claims
Application Information

- Generate Ideas
- Intellectual Property
- Life Sciences
- Materials
- Tech Scout
- Unparalleled Data Quality
- Higher Quality Content
- 60% Fewer Hallucinations
Browse by: Latest US Patents, China's latest patents, Technical Efficacy Thesaurus, Application Domain, Technology Topic, Popular Technical Reports.
© 2025 PatSnap. All rights reserved.Legal|Privacy policy|Modern Slavery Act Transparency Statement|Sitemap|About US| Contact US: help@patsnap.com