Production process of honeycomb plate for household appliance packaging
A production process and technology of honeycomb panels, applied in the field of honeycomb panel preparation, can solve the problems of insufficient strength of paper honeycomb cores, failure to protect household appliances from impact, and poor cushioning performance, so as to achieve enhanced protection, cost savings, and increased cushioning performance Effect
- Summary
- Abstract
- Description
- Claims
- Application Information
AI Technical Summary
Problems solved by technology
Method used
Image
Examples
Embodiment 1
[0028] Such as Figure 1 to Figure 6 As shown, a production process of honeycomb panels for home appliance packaging includes the following steps:
[0029] Step 1, cutting, use the cutting device to cut the facial paper according to the required size;
[0030] Step 2, feeding, the cut facial tissue is sent into the gluing device through the feeding device;
[0031] Step 3: Apply glue. The glue applicator applies glue to one side of the facial paper A1 and facial paper B2 respectively. Two paper card slots 3 are pasted on the glued surfaces of the facial paper A1 and facial paper B2, and then take two pieces The paper honeycomb core 4 is pasted on the glued surface of the face paper A1 and is located outside the two paper card slots 3 respectively;
[0032] Step 4: Composite facial paper, paste the glued surface of facial paper B2 on the outside of the honeycomb core 4 on facial paper A1 and require that the paper card slots 3 of facial paper A1 and facial paper B2 correspond...
Embodiment 2
[0040] A production process of a honeycomb panel for home appliance packaging, comprising the following steps:
[0041] Step 1, cutting, use the cutting device to cut the facial paper according to the required size;
[0042] Step 2, feeding, the cut facial tissue is sent into the gluing device through the feeding device;
[0043] Step 3: Apply glue. The glue applicator applies glue to one side of the facial paper A1 and facial paper B2 respectively. Two paper card slots 3 are pasted on the glued surfaces of the facial paper A1 and facial paper B2, and then take two pieces The paper honeycomb core 4 is pasted on the glued surface of the face paper A1 and is located outside the two paper card slots 3 respectively;
[0044] Step 4: Composite facial paper, paste the glued surface of facial paper B2 on the outside of the honeycomb core 4 on facial paper A1 and require that the paper card slots 3 of facial paper A1 and facial paper B2 correspond one by one. The facial paper B2 and...
PUM
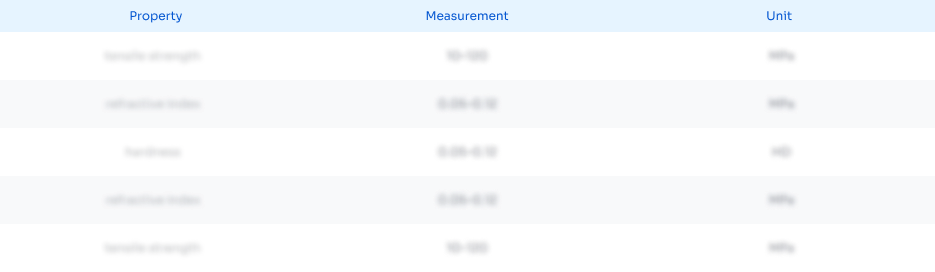
Abstract
Description
Claims
Application Information

- R&D
- Intellectual Property
- Life Sciences
- Materials
- Tech Scout
- Unparalleled Data Quality
- Higher Quality Content
- 60% Fewer Hallucinations
Browse by: Latest US Patents, China's latest patents, Technical Efficacy Thesaurus, Application Domain, Technology Topic, Popular Technical Reports.
© 2025 PatSnap. All rights reserved.Legal|Privacy policy|Modern Slavery Act Transparency Statement|Sitemap|About US| Contact US: help@patsnap.com