Manipulator device with stable clamping function
A manipulator and stable technology, applied in the field of manipulators, can solve the problems of affecting the production efficiency of workpieces, large clamping force, and small clamping force, and achieve the effect of convenient clamping, reasonable structure and protection of workpieces
- Summary
- Abstract
- Description
- Claims
- Application Information
AI Technical Summary
Problems solved by technology
Method used
Image
Examples
Embodiment 1
[0023] see Figure 1~4 , in the embodiment of the present invention, a manipulator device with stable clamping includes a motor frame 1, a fixed frame 5 and a fixed frame 10, a first motor 2 is installed inside the motor frame 1, and a first motor 2 is installed at the front end of the shaft of the first motor The first threaded rod 3, the first rolling bearing 4 is installed on the front end of the first threaded rod 3, the slider 6 is installed on the outside of the first threaded rod 3, the fixed frame 5 is installed on the front side of the motor frame 1, and the middle part of the slider 6 is provided with a screw hole , the inner side of the screw hole is meshed with the outer side of the first threaded rod 3, and the first rolling bearing 4 is installed at the connection between the first threaded rod 3 and the fixed frame 5; The shape is I-shaped; telescopic motor 8 is installed at the bottom of limit plate 7, fixed plate 9 is installed at the front end of telescopic m...
Embodiment 2
[0026] see Figure 5 , in the embodiment of the present invention, a manipulator device with stable clamping includes a motor frame 1, a fixed frame 5 and a fixed frame 10, a first motor 2 is installed inside the motor frame 1, and a first motor 2 is installed at the front end of the shaft of the first motor The first threaded rod 3, the first rolling bearing 4 is installed on the front end of the first threaded rod 3, the slider 6 is installed on the outside of the first threaded rod 4, the fixed frame 5 is installed on the front side of the motor frame 1; the bottom end of the slider 6 is installed with a limit Plate 7, telescopic motor 8 is installed on the bottom end of the limit plate 7, fixed plate 9 is installed on the front end of the telescopic motor 8, fixed frame 10 is installed on the left and right sides of the bottom end of the fixed plate 9, and the second motor is installed on the middle part of the bottom end of the fixed plate 9 11. The cross-sectional shape ...
PUM
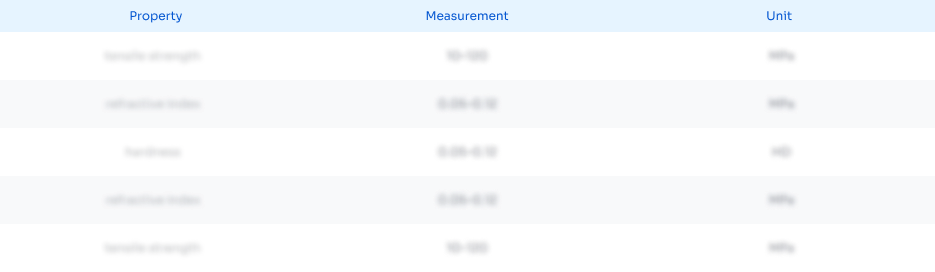
Abstract
Description
Claims
Application Information

- Generate Ideas
- Intellectual Property
- Life Sciences
- Materials
- Tech Scout
- Unparalleled Data Quality
- Higher Quality Content
- 60% Fewer Hallucinations
Browse by: Latest US Patents, China's latest patents, Technical Efficacy Thesaurus, Application Domain, Technology Topic, Popular Technical Reports.
© 2025 PatSnap. All rights reserved.Legal|Privacy policy|Modern Slavery Act Transparency Statement|Sitemap|About US| Contact US: help@patsnap.com