Magnetic levitation flywheel motor structure parameter optimization design method
A technology for structural parameters and flywheel motors, applied in the field of optimization design of magnetic levitation flywheel motor structural parameters, can solve the problems of reducing finite element models and low fitting accuracy
- Summary
- Abstract
- Description
- Claims
- Application Information
AI Technical Summary
Problems solved by technology
Method used
Image
Examples
Embodiment Construction
[0070] In order to deepen the understanding of the present invention, the present invention will be described in further detail below in conjunction with the accompanying drawings and embodiments, which are only used to explain the present invention and do not limit the protection scope of the present invention.
[0071] Among the present invention, dynamic double response surface method DRSM refers to Dual Response Surface Methodology;
[0072] A flow chart of the structural parameter optimization design method for a magnetic levitation flywheel motor proposed by the present invention is as attached figure 1 As shown, the main steps are as follows:
[0073] (1) Establish the motor finite element model according to the initial structural parameters of the motor, and determine the optimal performance parameters of the motor;
[0074] (2) Select the structural parameters to be optimized and their level factors, and establish a response surface (RSM) experiment schedule;
[007...
PUM
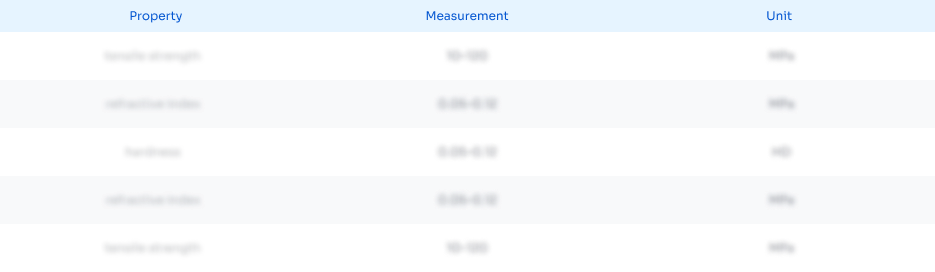
Abstract
Description
Claims
Application Information

- R&D Engineer
- R&D Manager
- IP Professional
- Industry Leading Data Capabilities
- Powerful AI technology
- Patent DNA Extraction
Browse by: Latest US Patents, China's latest patents, Technical Efficacy Thesaurus, Application Domain, Technology Topic, Popular Technical Reports.
© 2024 PatSnap. All rights reserved.Legal|Privacy policy|Modern Slavery Act Transparency Statement|Sitemap|About US| Contact US: help@patsnap.com