Battery pack
A battery and packaging technology, applied in the direction of batteries, battery pack components, circuits, etc., can solve the problems of useless space, energy density reduction, battery packaging size, weight increase, etc.
- Summary
- Abstract
- Description
- Claims
- Application Information
AI Technical Summary
Problems solved by technology
Method used
Image
Examples
no. 1 approach
[0053] Below, based on figure 1 A first embodiment of the present invention will be described.
[0054] The battery pack 11 is formed by joining a container-shaped battery case 12 with an open upper surface and a battery cover 13 closing the opening of the upper surface of the battery case 12 at respective flanges. Inside, the several square unit body 14... which has a rectangular parallelepiped shape is accommodated in the state laminated|stacked along the lamination direction. A plurality of stacked square cells 14 ... constitute a cell stack 15 , and in the present embodiment, two cell stacks 15 , 15 are accommodated in the battery case 12 in parallel. Each cell stack 15 is different from conventional battery modules in that a plurality of rectangular cells 14... are only stacked in a free state, and are not compressed in the stacking direction.
[0055] When the battery case 12 made of aluminum is manufactured by die casting, the first side wall 12a and the second side w...
no. 3 approach
[0066] Next, based on figure 2 The second and third embodiments of the present invention will be described.
[0067] The wedge member 19 of the first embodiment has bolt holes 19a, 19a through which the bolts 18, 18 pass. figure 2 The wedge member 19 of the second embodiment shown in (A) has long groove-shaped bolt grooves 19d, 19d opened on both sides in the longitudinal direction, and bolts 18, 18 are fitted into these bolt grooves 19d, 19d from the side. in addition, figure 2 The wedge member 19 of the third embodiment shown in (B) has long groove-shaped bolt grooves 19d, 19d opened on its first abutting surface 19b, and bolts 18, 18 are fitted into these bolt grooves 19d, 19d from the stacking direction. combine.
[0068] According to these embodiments, since the bolts 18, 18 do not pass through the bolt holes 19a, 19a, it is only necessary to fit the bolts 18, 18 into the bolt grooves 19d, 19d from the side or the stacking direction, so the The assembly work of the...
no. 4 approach
[0070] Next, based on image 3 A fourth embodiment of the present invention will be described.
[0071] In the battery package 11 of the fourth embodiment, a cell pressing mechanism 17 is arranged in the center of the battery case 12 in the stacking direction, and two end plates 20, 20 and two cell pressing mechanisms are respectively arranged on both sides of the battery case 12 in the stacking direction. Laminate 15, 15. The wedge member 19, the bolts 18, 18, and the female threaded parts 12d, 12d of the single-body pressing mechanism 17 are the same as those of the first embodiment, but end plates 20, 20 are disposed on both sides of the wedge member 19 in the stacking direction. It is different from the first embodiment.
[0072] The wedge member 19 has first abutting surfaces 19b, 19b on both sides in the stacking direction, and each end plate 20 has a first abutting surface 20a abutting on the first abutting surface 19b of the wedge member 19 and a single laminated bod...
PUM
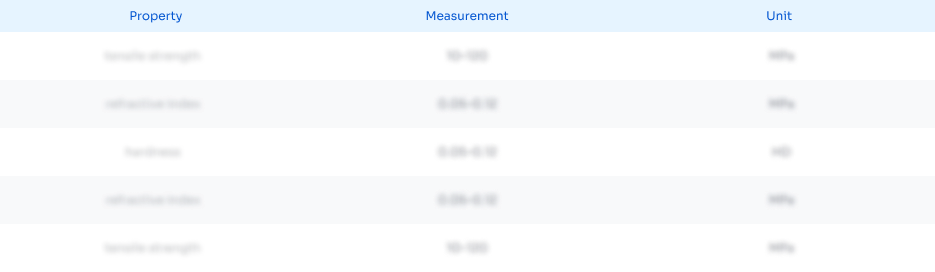
Abstract
Description
Claims
Application Information

- R&D
- Intellectual Property
- Life Sciences
- Materials
- Tech Scout
- Unparalleled Data Quality
- Higher Quality Content
- 60% Fewer Hallucinations
Browse by: Latest US Patents, China's latest patents, Technical Efficacy Thesaurus, Application Domain, Technology Topic, Popular Technical Reports.
© 2025 PatSnap. All rights reserved.Legal|Privacy policy|Modern Slavery Act Transparency Statement|Sitemap|About US| Contact US: help@patsnap.com